ಅರೆವಾಹಕ ಉತ್ಪಾದನಾ ಪ್ರಕ್ರಿಯೆಯಲ್ಲಿ ನಿರ್ಣಾಯಕ ಹಂತವಾಗಿ ವೇಫರ್ ಡೈಸಿಂಗ್ ತಂತ್ರಜ್ಞಾನವು ಚಿಪ್ ಕಾರ್ಯಕ್ಷಮತೆ, ಇಳುವರಿ ಮತ್ತು ಉತ್ಪಾದನಾ ವೆಚ್ಚಗಳಿಗೆ ನೇರವಾಗಿ ಸಂಬಂಧಿಸಿದೆ.
#01 ವೇಫರ್ ಡೈಸಿಂಗ್ನ ಹಿನ್ನೆಲೆ ಮತ್ತು ಮಹತ್ವ
೧.೧ ವೇಫರ್ ಡೈಸಿಂಗ್ ನ ವ್ಯಾಖ್ಯಾನ
ವೇಫರ್ ಡೈಸಿಂಗ್ (ಸ್ಕ್ರೈಬಿಂಗ್ ಎಂದೂ ಕರೆಯುತ್ತಾರೆ) ಅರೆವಾಹಕ ತಯಾರಿಕೆಯಲ್ಲಿ ಅತ್ಯಗತ್ಯ ಹಂತವಾಗಿದ್ದು, ಸಂಸ್ಕರಿಸಿದ ವೇಫರ್ಗಳನ್ನು ಬಹು ಪ್ರತ್ಯೇಕ ಡೈಗಳಾಗಿ ವಿಭಜಿಸುವ ಗುರಿಯನ್ನು ಹೊಂದಿದೆ. ಈ ಡೈಗಳು ಸಾಮಾನ್ಯವಾಗಿ ಸಂಪೂರ್ಣ ಸರ್ಕ್ಯೂಟ್ ಕಾರ್ಯವನ್ನು ಹೊಂದಿರುತ್ತವೆ ಮತ್ತು ಎಲೆಕ್ಟ್ರಾನಿಕ್ ಸಾಧನಗಳ ಉತ್ಪಾದನೆಯಲ್ಲಿ ಅಂತಿಮವಾಗಿ ಬಳಸಲಾಗುವ ಪ್ರಮುಖ ಅಂಶಗಳಾಗಿವೆ. ಚಿಪ್ ವಿನ್ಯಾಸಗಳು ಹೆಚ್ಚು ಸಂಕೀರ್ಣವಾಗುತ್ತಿದ್ದಂತೆ ಮತ್ತು ಆಯಾಮಗಳು ಕುಗ್ಗುತ್ತಲೇ ಇರುವುದರಿಂದ, ವೇಫರ್ ಡೈಸಿಂಗ್ ತಂತ್ರಜ್ಞಾನದ ನಿಖರತೆ ಮತ್ತು ದಕ್ಷತೆಯ ಅವಶ್ಯಕತೆಗಳು ಹೆಚ್ಚು ಕಠಿಣವಾಗುತ್ತಿವೆ.
ಪ್ರಾಯೋಗಿಕ ಕಾರ್ಯಾಚರಣೆಗಳಲ್ಲಿ, ವೇಫರ್ ಡೈಸಿಂಗ್ ಸಾಮಾನ್ಯವಾಗಿ ಪ್ರತಿ ಡೈ ಹಾಗೆಯೇ ಮತ್ತು ಸಂಪೂರ್ಣವಾಗಿ ಕಾರ್ಯನಿರ್ವಹಿಸುವಂತೆ ಖಚಿತಪಡಿಸಿಕೊಳ್ಳಲು ಡೈಮಂಡ್ ಬ್ಲೇಡ್ಗಳಂತಹ ಹೆಚ್ಚಿನ-ನಿಖರ ಸಾಧನಗಳನ್ನು ಬಳಸುತ್ತದೆ. ಪ್ರಮುಖ ಹಂತಗಳಲ್ಲಿ ಕತ್ತರಿಸುವ ಮೊದಲು ತಯಾರಿ, ಕತ್ತರಿಸುವ ಪ್ರಕ್ರಿಯೆಯಲ್ಲಿ ನಿಖರವಾದ ನಿಯಂತ್ರಣ ಮತ್ತು ಕತ್ತರಿಸಿದ ನಂತರ ಗುಣಮಟ್ಟದ ತಪಾಸಣೆ ಸೇರಿವೆ.
ಕತ್ತರಿಸುವ ಮೊದಲು, ನಿಖರವಾದ ಕತ್ತರಿಸುವ ಮಾರ್ಗಗಳನ್ನು ಖಚಿತಪಡಿಸಿಕೊಳ್ಳಲು ವೇಫರ್ ಅನ್ನು ಗುರುತಿಸಬೇಕು ಮತ್ತು ಇರಿಸಬೇಕು. ಕತ್ತರಿಸುವ ಸಮಯದಲ್ಲಿ, ವೇಫರ್ಗೆ ಹಾನಿಯಾಗದಂತೆ ತಡೆಯಲು ಉಪಕರಣದ ಒತ್ತಡ ಮತ್ತು ವೇಗದಂತಹ ನಿಯತಾಂಕಗಳನ್ನು ಕಟ್ಟುನಿಟ್ಟಾಗಿ ನಿಯಂತ್ರಿಸಬೇಕು. ಕತ್ತರಿಸಿದ ನಂತರ, ಪ್ರತಿ ಚಿಪ್ ಕಾರ್ಯಕ್ಷಮತೆಯ ಮಾನದಂಡಗಳನ್ನು ಪೂರೈಸುತ್ತದೆ ಎಂದು ಖಚಿತಪಡಿಸಿಕೊಳ್ಳಲು ಸಮಗ್ರ ಗುಣಮಟ್ಟದ ತಪಾಸಣೆಗಳನ್ನು ನಡೆಸಲಾಗುತ್ತದೆ.
ವೇಫರ್ ಡೈಸಿಂಗ್ ತಂತ್ರಜ್ಞಾನದ ಮೂಲಭೂತ ತತ್ವಗಳು ಕತ್ತರಿಸುವ ಉಪಕರಣಗಳ ಆಯ್ಕೆ ಮತ್ತು ಪ್ರಕ್ರಿಯೆಯ ನಿಯತಾಂಕಗಳ ಸೆಟ್ಟಿಂಗ್ ಮಾತ್ರವಲ್ಲದೆ ಕತ್ತರಿಸುವ ಗುಣಮಟ್ಟದ ಮೇಲೆ ವಸ್ತುಗಳ ಯಾಂತ್ರಿಕ ಗುಣಲಕ್ಷಣಗಳು ಮತ್ತು ಗುಣಲಕ್ಷಣಗಳ ಪ್ರಭಾವವನ್ನು ಸಹ ಒಳಗೊಂಡಿದೆ. ಉದಾಹರಣೆಗೆ, ಕಡಿಮೆ-ಕೆ ಡೈಎಲೆಕ್ಟ್ರಿಕ್ ಸಿಲಿಕಾನ್ ವೇಫರ್ಗಳು, ಅವುಗಳ ಕೆಳಮಟ್ಟದ ಯಾಂತ್ರಿಕ ಗುಣಲಕ್ಷಣಗಳಿಂದಾಗಿ, ಕತ್ತರಿಸುವ ಸಮಯದಲ್ಲಿ ಒತ್ತಡದ ಸಾಂದ್ರತೆಗೆ ಹೆಚ್ಚು ಒಳಗಾಗುತ್ತವೆ, ಇದು ಚಿಪ್ಪಿಂಗ್ ಮತ್ತು ಬಿರುಕುಗೊಳಿಸುವಿಕೆಯಂತಹ ವೈಫಲ್ಯಗಳಿಗೆ ಕಾರಣವಾಗುತ್ತದೆ. ಕಡಿಮೆ-ಕೆ ವಸ್ತುಗಳ ಕಡಿಮೆ ಗಡಸುತನ ಮತ್ತು ದುರ್ಬಲತೆಯು ಯಾಂತ್ರಿಕ ಬಲ ಅಥವಾ ಉಷ್ಣ ಒತ್ತಡದ ಅಡಿಯಲ್ಲಿ, ವಿಶೇಷವಾಗಿ ಕತ್ತರಿಸುವ ಸಮಯದಲ್ಲಿ ರಚನಾತ್ಮಕ ಹಾನಿಗೆ ಹೆಚ್ಚು ಒಳಗಾಗುವಂತೆ ಮಾಡುತ್ತದೆ. ಉಪಕರಣ ಮತ್ತು ವೇಫರ್ ಮೇಲ್ಮೈ ನಡುವಿನ ಸಂಪರ್ಕವು ಹೆಚ್ಚಿನ ತಾಪಮಾನದೊಂದಿಗೆ ಸೇರಿಕೊಂಡು, ಒತ್ತಡದ ಸಾಂದ್ರತೆಯನ್ನು ಮತ್ತಷ್ಟು ಉಲ್ಬಣಗೊಳಿಸಬಹುದು.
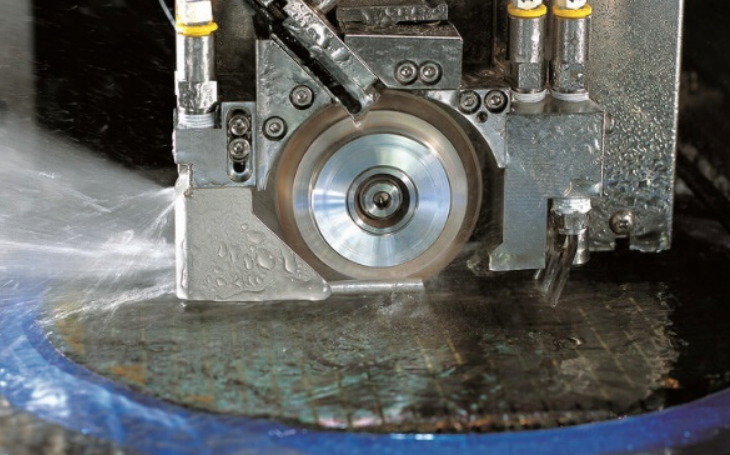
ವಸ್ತು ವಿಜ್ಞಾನದಲ್ಲಿನ ಪ್ರಗತಿಯೊಂದಿಗೆ, ವೇಫರ್ ಡೈಸಿಂಗ್ ತಂತ್ರಜ್ಞಾನವು ಸಾಂಪ್ರದಾಯಿಕ ಸಿಲಿಕಾನ್-ಆಧಾರಿತ ಅರೆವಾಹಕಗಳನ್ನು ಮೀರಿ ಗ್ಯಾಲಿಯಮ್ ನೈಟ್ರೈಡ್ (GaN) ನಂತಹ ಹೊಸ ವಸ್ತುಗಳನ್ನು ಸೇರಿಸಲು ವಿಸ್ತರಿಸಿದೆ. ಈ ಹೊಸ ವಸ್ತುಗಳು, ಅವುಗಳ ಗಡಸುತನ ಮತ್ತು ರಚನಾತ್ಮಕ ಗುಣಲಕ್ಷಣಗಳಿಂದಾಗಿ, ಡೈಸಿಂಗ್ ಪ್ರಕ್ರಿಯೆಗಳಿಗೆ ಹೊಸ ಸವಾಲುಗಳನ್ನು ಒಡ್ಡುತ್ತವೆ, ಕತ್ತರಿಸುವ ಉಪಕರಣಗಳು ಮತ್ತು ತಂತ್ರಗಳಲ್ಲಿ ಮತ್ತಷ್ಟು ಸುಧಾರಣೆಗಳ ಅಗತ್ಯವಿರುತ್ತದೆ.
ಅರೆವಾಹಕ ಉದ್ಯಮದಲ್ಲಿ ನಿರ್ಣಾಯಕ ಪ್ರಕ್ರಿಯೆಯಾಗಿ, ವಿಕಸನಗೊಳ್ಳುತ್ತಿರುವ ಬೇಡಿಕೆಗಳು ಮತ್ತು ತಾಂತ್ರಿಕ ಪ್ರಗತಿಗಳಿಗೆ ಪ್ರತಿಕ್ರಿಯೆಯಾಗಿ ವೇಫರ್ ಡೈಸಿಂಗ್ ಅನ್ನು ಅತ್ಯುತ್ತಮವಾಗಿಸಲಾಗುತ್ತಿದೆ, ಭವಿಷ್ಯದ ಮೈಕ್ರೋಎಲೆಕ್ಟ್ರಾನಿಕ್ಸ್ ಮತ್ತು ಇಂಟಿಗ್ರೇಟೆಡ್ ಸರ್ಕ್ಯೂಟ್ ತಂತ್ರಜ್ಞಾನಗಳಿಗೆ ಅಡಿಪಾಯ ಹಾಕಲಾಗುತ್ತಿದೆ.
ವೇಫರ್ ಡೈಸಿಂಗ್ ತಂತ್ರಜ್ಞಾನದಲ್ಲಿನ ಸುಧಾರಣೆಗಳು ಸಹಾಯಕ ವಸ್ತುಗಳು ಮತ್ತು ಪರಿಕರಗಳ ಅಭಿವೃದ್ಧಿಯನ್ನು ಮೀರಿವೆ. ಅವು ಪ್ರಕ್ರಿಯೆಯ ಆಪ್ಟಿಮೈಸೇಶನ್, ಸಲಕರಣೆಗಳ ಕಾರ್ಯಕ್ಷಮತೆಯಲ್ಲಿ ವರ್ಧನೆಗಳು ಮತ್ತು ಡೈಸಿಂಗ್ ನಿಯತಾಂಕಗಳ ನಿಖರವಾದ ನಿಯಂತ್ರಣವನ್ನು ಸಹ ಒಳಗೊಂಡಿವೆ. ಈ ಪ್ರಗತಿಗಳು ವೇಫರ್ ಡೈಸಿಂಗ್ ಪ್ರಕ್ರಿಯೆಯಲ್ಲಿ ಹೆಚ್ಚಿನ ನಿಖರತೆ, ದಕ್ಷತೆ ಮತ್ತು ಸ್ಥಿರತೆಯನ್ನು ಖಚಿತಪಡಿಸಿಕೊಳ್ಳುವ ಗುರಿಯನ್ನು ಹೊಂದಿವೆ, ಸಣ್ಣ ಆಯಾಮಗಳು, ಹೆಚ್ಚಿನ ಏಕೀಕರಣ ಮತ್ತು ಹೆಚ್ಚು ಸಂಕೀರ್ಣವಾದ ಚಿಪ್ ರಚನೆಗಳಿಗಾಗಿ ಅರೆವಾಹಕ ಉದ್ಯಮದ ಅಗತ್ಯವನ್ನು ಪೂರೈಸುತ್ತವೆ.
ಅಭಿವೃದ್ಧಿ ಪ್ರದೇಶ | ನಿರ್ದಿಷ್ಟ ಕ್ರಮಗಳು | ಪರಿಣಾಮಗಳು |
ಪ್ರಕ್ರಿಯೆ ಅತ್ಯುತ್ತಮೀಕರಣ | - ಹೆಚ್ಚು ನಿಖರವಾದ ವೇಫರ್ ಸ್ಥಾನೀಕರಣ ಮತ್ತು ಮಾರ್ಗ ಯೋಜನೆ ಮುಂತಾದ ಆರಂಭಿಕ ಸಿದ್ಧತೆಗಳನ್ನು ಸುಧಾರಿಸಿ. | - ಕತ್ತರಿಸುವ ದೋಷಗಳನ್ನು ಕಡಿಮೆ ಮಾಡಿ ಮತ್ತು ಸ್ಥಿರತೆಯನ್ನು ಸುಧಾರಿಸಿ. |
- ಕತ್ತರಿಸುವ ದೋಷಗಳನ್ನು ಕಡಿಮೆ ಮಾಡಿ ಮತ್ತು ಸ್ಥಿರತೆಯನ್ನು ಹೆಚ್ಚಿಸಿ. | - ಉಪಕರಣದ ಒತ್ತಡ, ವೇಗ ಮತ್ತು ತಾಪಮಾನವನ್ನು ಸರಿಹೊಂದಿಸಲು ನೈಜ-ಸಮಯದ ಮೇಲ್ವಿಚಾರಣೆ ಮತ್ತು ಪ್ರತಿಕ್ರಿಯೆ ಕಾರ್ಯವಿಧಾನಗಳನ್ನು ಅಳವಡಿಸಿಕೊಳ್ಳಿ. | |
- ವೇಫರ್ ಒಡೆಯುವಿಕೆಯ ದರಗಳನ್ನು ಕಡಿಮೆ ಮಾಡಿ ಮತ್ತು ಚಿಪ್ ಗುಣಮಟ್ಟವನ್ನು ಸುಧಾರಿಸಿ. | ||
ಸಲಕರಣೆಗಳ ಕಾರ್ಯಕ್ಷಮತೆ ವರ್ಧನೆ | - ಹೆಚ್ಚಿನ ನಿಖರತೆಯ ಯಾಂತ್ರಿಕ ವ್ಯವಸ್ಥೆಗಳು ಮತ್ತು ಸುಧಾರಿತ ಯಾಂತ್ರೀಕೃತಗೊಂಡ ನಿಯಂತ್ರಣ ತಂತ್ರಜ್ಞಾನವನ್ನು ಬಳಸಿಕೊಳ್ಳಿ. | - ಕತ್ತರಿಸುವ ನಿಖರತೆಯನ್ನು ಹೆಚ್ಚಿಸಿ ಮತ್ತು ವಸ್ತು ವ್ಯರ್ಥವನ್ನು ಕಡಿಮೆ ಮಾಡಿ. |
- ಹೆಚ್ಚಿನ ಗಡಸುತನದ ವಸ್ತು ವೇಫರ್ಗಳಿಗೆ ಸೂಕ್ತವಾದ ಲೇಸರ್ ಕತ್ತರಿಸುವ ತಂತ್ರಜ್ಞಾನವನ್ನು ಪರಿಚಯಿಸಿ. | - ಉತ್ಪಾದನಾ ದಕ್ಷತೆಯನ್ನು ಸುಧಾರಿಸಿ ಮತ್ತು ಹಸ್ತಚಾಲಿತ ದೋಷಗಳನ್ನು ಕಡಿಮೆ ಮಾಡಿ. | |
- ಸ್ವಯಂಚಾಲಿತ ಮೇಲ್ವಿಚಾರಣೆ ಮತ್ತು ಹೊಂದಾಣಿಕೆಗಳಿಗಾಗಿ ಸಲಕರಣೆಗಳ ಯಾಂತ್ರೀಕರಣವನ್ನು ಹೆಚ್ಚಿಸಿ. | ||
ನಿಖರವಾದ ನಿಯತಾಂಕ ನಿಯಂತ್ರಣ | - ಕತ್ತರಿಸುವ ಆಳ, ವೇಗ, ಉಪಕರಣದ ಪ್ರಕಾರ ಮತ್ತು ತಂಪಾಗಿಸುವ ವಿಧಾನಗಳಂತಹ ನಿಯತಾಂಕಗಳನ್ನು ಸೂಕ್ಷ್ಮವಾಗಿ ಹೊಂದಿಸಿ. | - ಡೈ ಸಮಗ್ರತೆ ಮತ್ತು ವಿದ್ಯುತ್ ಕಾರ್ಯಕ್ಷಮತೆಯನ್ನು ಖಚಿತಪಡಿಸಿಕೊಳ್ಳಿ. |
- ವೇಫರ್ ವಸ್ತು, ದಪ್ಪ ಮತ್ತು ರಚನೆಯ ಆಧಾರದ ಮೇಲೆ ನಿಯತಾಂಕಗಳನ್ನು ಕಸ್ಟಮೈಸ್ ಮಾಡಿ. | - ಇಳುವರಿ ದರಗಳನ್ನು ಹೆಚ್ಚಿಸಿ, ವಸ್ತು ತ್ಯಾಜ್ಯವನ್ನು ಕಡಿಮೆ ಮಾಡಿ ಮತ್ತು ಉತ್ಪಾದನಾ ವೆಚ್ಚವನ್ನು ಕಡಿಮೆ ಮಾಡಿ. | |
ಕಾರ್ಯತಂತ್ರದ ಮಹತ್ವ | - ಮಾರುಕಟ್ಟೆ ಬೇಡಿಕೆಗಳನ್ನು ಪೂರೈಸಲು ಹೊಸ ತಾಂತ್ರಿಕ ಮಾರ್ಗಗಳನ್ನು ನಿರಂತರವಾಗಿ ಅನ್ವೇಷಿಸಿ, ಪ್ರಕ್ರಿಯೆಗಳನ್ನು ಅತ್ಯುತ್ತಮವಾಗಿಸಿ ಮತ್ತು ಸಲಕರಣೆಗಳ ಸಾಮರ್ಥ್ಯಗಳನ್ನು ಹೆಚ್ಚಿಸಿ. | - ಚಿಪ್ ಉತ್ಪಾದನಾ ಇಳುವರಿ ಮತ್ತು ಕಾರ್ಯಕ್ಷಮತೆಯನ್ನು ಸುಧಾರಿಸಿ, ಹೊಸ ವಸ್ತುಗಳು ಮತ್ತು ಸುಧಾರಿತ ಚಿಪ್ ವಿನ್ಯಾಸಗಳ ಅಭಿವೃದ್ಧಿಯನ್ನು ಬೆಂಬಲಿಸಿ. |
೧.೨ ವೇಫರ್ ಡೈಸಿಂಗ್ನ ಪ್ರಾಮುಖ್ಯತೆ
ಅರೆವಾಹಕ ಉತ್ಪಾದನಾ ಪ್ರಕ್ರಿಯೆಯಲ್ಲಿ ವೇಫರ್ ಡೈಸಿಂಗ್ ನಿರ್ಣಾಯಕ ಪಾತ್ರವನ್ನು ವಹಿಸುತ್ತದೆ, ಇದು ನಂತರದ ಹಂತಗಳ ಮೇಲೆ ಹಾಗೂ ಅಂತಿಮ ಉತ್ಪನ್ನದ ಗುಣಮಟ್ಟ ಮತ್ತು ಕಾರ್ಯಕ್ಷಮತೆಯ ಮೇಲೆ ನೇರವಾಗಿ ಪರಿಣಾಮ ಬೀರುತ್ತದೆ. ಇದರ ಮಹತ್ವವನ್ನು ಈ ಕೆಳಗಿನಂತೆ ವಿವರಿಸಬಹುದು:
ಮೊದಲನೆಯದಾಗಿ, ಚಿಪ್ ಇಳುವರಿ ಮತ್ತು ವಿಶ್ವಾಸಾರ್ಹತೆಯನ್ನು ಖಚಿತಪಡಿಸಿಕೊಳ್ಳಲು ಡೈಸಿಂಗ್ನ ನಿಖರತೆ ಮತ್ತು ಸ್ಥಿರತೆ ಪ್ರಮುಖವಾಗಿದೆ. ತಯಾರಿಕೆಯ ಸಮಯದಲ್ಲಿ, ವೇಫರ್ಗಳು ಹಲವಾರು ಸಂಕೀರ್ಣ ಸರ್ಕ್ಯೂಟ್ ರಚನೆಗಳನ್ನು ರೂಪಿಸಲು ಬಹು ಸಂಸ್ಕರಣಾ ಹಂತಗಳಿಗೆ ಒಳಗಾಗುತ್ತವೆ, ಇವುಗಳನ್ನು ನಿಖರವಾಗಿ ಪ್ರತ್ಯೇಕ ಚಿಪ್ಗಳಾಗಿ ವಿಂಗಡಿಸಬೇಕು (ಡೈಸ್). ಡೈಸಿಂಗ್ ಪ್ರಕ್ರಿಯೆಯ ಸಮಯದಲ್ಲಿ ಜೋಡಣೆ ಅಥವಾ ಕತ್ತರಿಸುವಲ್ಲಿ ಗಮನಾರ್ಹ ದೋಷಗಳಿದ್ದರೆ, ಸರ್ಕ್ಯೂಟ್ಗಳು ಹಾನಿಗೊಳಗಾಗಬಹುದು, ಇದು ಚಿಪ್ನ ಕಾರ್ಯಕ್ಷಮತೆ ಮತ್ತು ವಿಶ್ವಾಸಾರ್ಹತೆಯ ಮೇಲೆ ಪರಿಣಾಮ ಬೀರುತ್ತದೆ. ಆದ್ದರಿಂದ, ಹೆಚ್ಚಿನ ನಿಖರವಾದ ಡೈಸಿಂಗ್ ತಂತ್ರಜ್ಞಾನವು ಪ್ರತಿ ಚಿಪ್ನ ಸಮಗ್ರತೆಯನ್ನು ಖಚಿತಪಡಿಸುವುದಲ್ಲದೆ, ಆಂತರಿಕ ಸರ್ಕ್ಯೂಟ್ಗಳಿಗೆ ಹಾನಿಯಾಗದಂತೆ ತಡೆಯುತ್ತದೆ, ಒಟ್ಟಾರೆ ಇಳುವರಿ ದರವನ್ನು ಸುಧಾರಿಸುತ್ತದೆ.
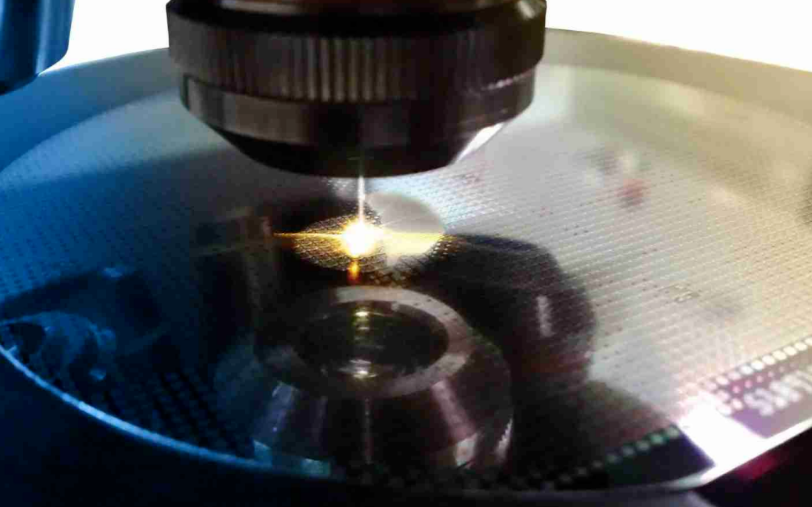
ಎರಡನೆಯದಾಗಿ, ವೇಫರ್ ಡೈಸಿಂಗ್ ಉತ್ಪಾದನಾ ದಕ್ಷತೆ ಮತ್ತು ವೆಚ್ಚ ನಿಯಂತ್ರಣದ ಮೇಲೆ ಗಮನಾರ್ಹ ಪರಿಣಾಮ ಬೀರುತ್ತದೆ. ಉತ್ಪಾದನಾ ಪ್ರಕ್ರಿಯೆಯಲ್ಲಿ ನಿರ್ಣಾಯಕ ಹಂತವಾಗಿ, ಅದರ ದಕ್ಷತೆಯು ನಂತರದ ಹಂತಗಳ ಪ್ರಗತಿಯ ಮೇಲೆ ನೇರವಾಗಿ ಪರಿಣಾಮ ಬೀರುತ್ತದೆ. ಡೈಸಿಂಗ್ ಪ್ರಕ್ರಿಯೆಯನ್ನು ಅತ್ಯುತ್ತಮವಾಗಿಸುವ ಮೂಲಕ, ಯಾಂತ್ರೀಕೃತಗೊಂಡ ಮಟ್ಟವನ್ನು ಹೆಚ್ಚಿಸುವ ಮೂಲಕ ಮತ್ತು ಕತ್ತರಿಸುವ ವೇಗವನ್ನು ಸುಧಾರಿಸುವ ಮೂಲಕ, ಒಟ್ಟಾರೆ ಉತ್ಪಾದನಾ ದಕ್ಷತೆಯನ್ನು ಹೆಚ್ಚು ಹೆಚ್ಚಿಸಬಹುದು.
ಮತ್ತೊಂದೆಡೆ, ಡೈಸಿಂಗ್ ಸಮಯದಲ್ಲಿ ವಸ್ತು ವ್ಯರ್ಥವಾಗುವುದು ವೆಚ್ಚ ನಿರ್ವಹಣೆಯಲ್ಲಿ ನಿರ್ಣಾಯಕ ಅಂಶವಾಗಿದೆ. ಸುಧಾರಿತ ಡೈಸಿಂಗ್ ತಂತ್ರಜ್ಞಾನಗಳನ್ನು ಬಳಸುವುದರಿಂದ ಕತ್ತರಿಸುವ ಪ್ರಕ್ರಿಯೆಯಲ್ಲಿ ಅನಗತ್ಯ ವಸ್ತು ನಷ್ಟವನ್ನು ಕಡಿಮೆ ಮಾಡುವುದಲ್ಲದೆ, ವೇಫರ್ ಬಳಕೆಯನ್ನು ಹೆಚ್ಚಿಸುತ್ತದೆ, ಇದರಿಂದಾಗಿ ಉತ್ಪಾದನಾ ವೆಚ್ಚವನ್ನು ಕಡಿಮೆ ಮಾಡುತ್ತದೆ.
ಅರೆವಾಹಕ ತಂತ್ರಜ್ಞಾನದಲ್ಲಿನ ಪ್ರಗತಿಯೊಂದಿಗೆ, ವೇಫರ್ ವ್ಯಾಸಗಳು ಹೆಚ್ಚುತ್ತಲೇ ಇರುತ್ತವೆ ಮತ್ತು ಸರ್ಕ್ಯೂಟ್ ಸಾಂದ್ರತೆಗಳು ಅದಕ್ಕೆ ಅನುಗುಣವಾಗಿ ಹೆಚ್ಚಾಗುತ್ತವೆ, ಇದು ಡೈಸಿಂಗ್ ತಂತ್ರಜ್ಞಾನದ ಮೇಲೆ ಹೆಚ್ಚಿನ ಬೇಡಿಕೆಗಳನ್ನು ಇರಿಸುತ್ತದೆ. ದೊಡ್ಡ ವೇಫರ್ಗಳಿಗೆ ಕತ್ತರಿಸುವ ಮಾರ್ಗಗಳ ಹೆಚ್ಚು ನಿಖರವಾದ ನಿಯಂತ್ರಣದ ಅಗತ್ಯವಿರುತ್ತದೆ, ವಿಶೇಷವಾಗಿ ಹೆಚ್ಚಿನ ಸಾಂದ್ರತೆಯ ಸರ್ಕ್ಯೂಟ್ ಪ್ರದೇಶಗಳಲ್ಲಿ, ಅಲ್ಲಿ ಸಣ್ಣ ವಿಚಲನಗಳು ಸಹ ಬಹು ಚಿಪ್ಗಳನ್ನು ದೋಷಯುಕ್ತವಾಗಿಸಬಹುದು. ಹೆಚ್ಚುವರಿಯಾಗಿ, ದೊಡ್ಡ ವೇಫರ್ಗಳು ಹೆಚ್ಚು ಕತ್ತರಿಸುವ ರೇಖೆಗಳು ಮತ್ತು ಹೆಚ್ಚು ಸಂಕೀರ್ಣ ಪ್ರಕ್ರಿಯೆಯ ಹಂತಗಳನ್ನು ಒಳಗೊಂಡಿರುತ್ತವೆ, ಈ ಸವಾಲುಗಳನ್ನು ಪೂರೈಸಲು ಡೈಸಿಂಗ್ ತಂತ್ರಜ್ಞಾನಗಳ ನಿಖರತೆ, ಸ್ಥಿರತೆ ಮತ್ತು ದಕ್ಷತೆಯಲ್ಲಿ ಮತ್ತಷ್ಟು ಸುಧಾರಣೆಗಳ ಅಗತ್ಯವಿರುತ್ತದೆ.
೧.೩ ವೇಫರ್ ಡೈಸಿಂಗ್ ಪ್ರಕ್ರಿಯೆ
ವೇಫರ್ ಡೈಸಿಂಗ್ ಪ್ರಕ್ರಿಯೆಯು ತಯಾರಿ ಹಂತದಿಂದ ಅಂತಿಮ ಗುಣಮಟ್ಟದ ಪರಿಶೀಲನೆಯವರೆಗಿನ ಎಲ್ಲಾ ಹಂತಗಳನ್ನು ಒಳಗೊಂಡಿದೆ, ಪ್ರತಿಯೊಂದು ಹಂತವು ಚೌಕವಾಗಿ ಕತ್ತರಿಸಿದ ಚಿಪ್ಗಳ ಗುಣಮಟ್ಟ ಮತ್ತು ಕಾರ್ಯಕ್ಷಮತೆಯನ್ನು ಖಚಿತಪಡಿಸಿಕೊಳ್ಳಲು ನಿರ್ಣಾಯಕವಾಗಿದೆ. ಕೆಳಗೆ ಪ್ರತಿಯೊಂದು ಹಂತದ ವಿವರವಾದ ವಿವರಣೆಯಿದೆ.
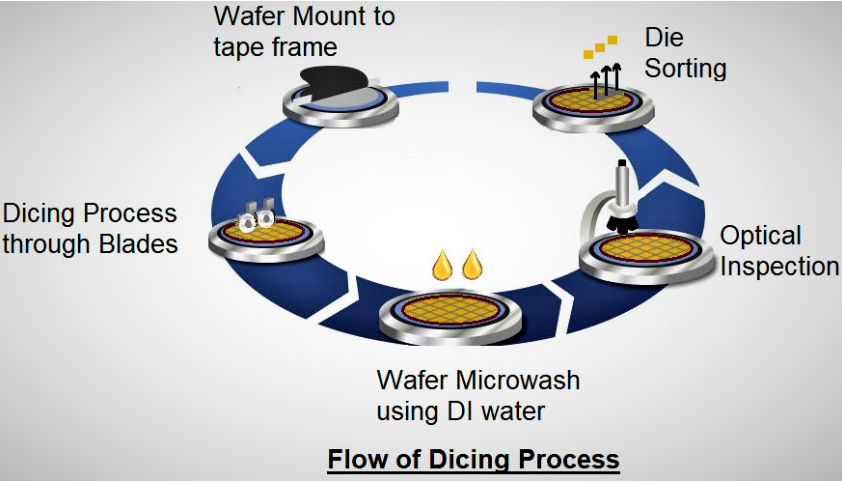
ಹಂತ | ವಿವರವಾದ ವಿವರಣೆ |
ತಯಾರಿ ಹಂತ | -ವೇಫರ್ ಶುಚಿಗೊಳಿಸುವಿಕೆ: ಕಲ್ಮಶಗಳು, ಕಣಗಳು ಮತ್ತು ಮಾಲಿನ್ಯಕಾರಕಗಳನ್ನು ತೆಗೆದುಹಾಕಲು, ಶುದ್ಧ ಮೇಲ್ಮೈಯನ್ನು ಖಚಿತಪಡಿಸಿಕೊಳ್ಳಲು, ಹೆಚ್ಚಿನ ಶುದ್ಧತೆಯ ನೀರು ಮತ್ತು ವಿಶೇಷ ಶುಚಿಗೊಳಿಸುವ ಏಜೆಂಟ್ಗಳನ್ನು ಅಲ್ಟ್ರಾಸಾನಿಕ್ ಅಥವಾ ಯಾಂತ್ರಿಕ ಸ್ಕ್ರಬ್ಬಿಂಗ್ನೊಂದಿಗೆ ಸಂಯೋಜಿಸಿ. -ನಿಖರವಾದ ಸ್ಥಾನೀಕರಣ: ವಿನ್ಯಾಸಗೊಳಿಸಿದ ಕತ್ತರಿಸುವ ಮಾರ್ಗಗಳಲ್ಲಿ ವೇಫರ್ ಅನ್ನು ನಿಖರವಾಗಿ ವಿಂಗಡಿಸಲಾಗಿದೆ ಎಂದು ಖಚಿತಪಡಿಸಿಕೊಳ್ಳಲು ಹೆಚ್ಚಿನ ನಿಖರತೆಯ ಉಪಕರಣಗಳನ್ನು ಬಳಸಿಕೊಳ್ಳಿ. -ವೇಫರ್ ಫಿಕ್ಸೇಶನ್: ಕತ್ತರಿಸುವಾಗ ಸ್ಥಿರತೆಯನ್ನು ಕಾಪಾಡಿಕೊಳ್ಳಲು, ಕಂಪನ ಅಥವಾ ಚಲನೆಯಿಂದ ಹಾನಿಯನ್ನು ತಡೆಗಟ್ಟಲು ವೇಫರ್ ಅನ್ನು ಟೇಪ್ ಫ್ರೇಮ್ಗೆ ಸುರಕ್ಷಿತಗೊಳಿಸಿ. |
ಕತ್ತರಿಸುವ ಹಂತ | -ಬ್ಲೇಡ್ ಡೈಸಿಂಗ್: ಭೌತಿಕ ಕತ್ತರಿಸುವಿಕೆಗಾಗಿ ಹೆಚ್ಚಿನ ವೇಗದಲ್ಲಿ ತಿರುಗುವ ವಜ್ರ-ಲೇಪಿತ ಬ್ಲೇಡ್ಗಳನ್ನು ಬಳಸಿ, ಸಿಲಿಕಾನ್ ಆಧಾರಿತ ವಸ್ತುಗಳಿಗೆ ಸೂಕ್ತವಾಗಿದೆ ಮತ್ತು ವೆಚ್ಚ-ಪರಿಣಾಮಕಾರಿ. -ಲೇಸರ್ ಡೈಸಿಂಗ್: ಸಂಪರ್ಕವಿಲ್ಲದ ಕತ್ತರಿಸುವಿಕೆಗೆ ಹೆಚ್ಚಿನ ಶಕ್ತಿಯ ಲೇಸರ್ ಕಿರಣಗಳನ್ನು ಬಳಸಿಕೊಳ್ಳಿ, ಗ್ಯಾಲಿಯಮ್ ನೈಟ್ರೈಡ್ನಂತಹ ಸುಲಭವಾಗಿ ಅಥವಾ ಹೆಚ್ಚಿನ ಗಡಸುತನದ ವಸ್ತುಗಳಿಗೆ ಸೂಕ್ತವಾಗಿದೆ, ಇದು ಹೆಚ್ಚಿನ ನಿಖರತೆ ಮತ್ತು ಕಡಿಮೆ ವಸ್ತು ನಷ್ಟವನ್ನು ನೀಡುತ್ತದೆ. -ಹೊಸ ತಂತ್ರಜ್ಞಾನಗಳು: ಶಾಖ-ಪೀಡಿತ ವಲಯಗಳನ್ನು ಕಡಿಮೆ ಮಾಡುವಾಗ ದಕ್ಷತೆ ಮತ್ತು ನಿಖರತೆಯನ್ನು ಮತ್ತಷ್ಟು ಸುಧಾರಿಸಲು ಲೇಸರ್ ಮತ್ತು ಪ್ಲಾಸ್ಮಾ ಕತ್ತರಿಸುವ ತಂತ್ರಜ್ಞಾನಗಳನ್ನು ಪರಿಚಯಿಸಿ. |
ಶುಚಿಗೊಳಿಸುವ ಹಂತ | - ಕತ್ತರಿಸುವಾಗ ಉತ್ಪತ್ತಿಯಾಗುವ ಭಗ್ನಾವಶೇಷಗಳು ಮತ್ತು ಧೂಳನ್ನು ತೆಗೆದುಹಾಕಲು, ನಂತರದ ಪ್ರಕ್ರಿಯೆಗಳು ಅಥವಾ ಚಿಪ್ ವಿದ್ಯುತ್ ಕಾರ್ಯಕ್ಷಮತೆಯ ಮೇಲೆ ಪರಿಣಾಮ ಬೀರುವ ಅವಶೇಷಗಳನ್ನು ತಡೆಯಲು, ಅಯಾನೀಕರಿಸಿದ ನೀರು (DI ನೀರು) ಮತ್ತು ವಿಶೇಷ ಶುಚಿಗೊಳಿಸುವ ಏಜೆಂಟ್ಗಳನ್ನು ಅಲ್ಟ್ರಾಸಾನಿಕ್ ಅಥವಾ ಸ್ಪ್ರೇ ಶುಚಿಗೊಳಿಸುವಿಕೆಯೊಂದಿಗೆ ಬಳಸಿ. - ಹೆಚ್ಚಿನ ಶುದ್ಧತೆಯ DI ನೀರು ಹೊಸ ಮಾಲಿನ್ಯಕಾರಕಗಳನ್ನು ಪರಿಚಯಿಸುವುದನ್ನು ತಪ್ಪಿಸುತ್ತದೆ, ಶುದ್ಧ ವೇಫರ್ ಪರಿಸರವನ್ನು ಖಚಿತಪಡಿಸುತ್ತದೆ. |
ತಪಾಸಣೆ ಹಂತ | -ಆಪ್ಟಿಕಲ್ ತಪಾಸಣೆ: ದೋಷಗಳನ್ನು ತ್ವರಿತವಾಗಿ ಗುರುತಿಸಲು, ಕತ್ತರಿಸಿದ ಚಿಪ್ಗಳಲ್ಲಿ ಯಾವುದೇ ಬಿರುಕುಗಳು ಅಥವಾ ಚಿಪ್ಪಿಂಗ್ ಇಲ್ಲ ಎಂದು ಖಚಿತಪಡಿಸಿಕೊಳ್ಳಲು, ತಪಾಸಣೆ ದಕ್ಷತೆಯನ್ನು ಸುಧಾರಿಸಲು ಮತ್ತು ಮಾನವ ದೋಷವನ್ನು ಕಡಿಮೆ ಮಾಡಲು AI ಅಲ್ಗಾರಿದಮ್ಗಳೊಂದಿಗೆ ಸಂಯೋಜಿಸಲ್ಪಟ್ಟ ಆಪ್ಟಿಕಲ್ ಪತ್ತೆ ವ್ಯವಸ್ಥೆಗಳನ್ನು ಬಳಸಿ. -ಆಯಾಮ ಮಾಪನ: ಚಿಪ್ ಆಯಾಮಗಳು ವಿನ್ಯಾಸದ ವಿಶೇಷಣಗಳನ್ನು ಪೂರೈಸುತ್ತವೆಯೇ ಎಂದು ಪರಿಶೀಲಿಸಿ. -ವಿದ್ಯುತ್ ಕಾರ್ಯಕ್ಷಮತೆ ಪರೀಕ್ಷೆ: ನಿರ್ಣಾಯಕ ಚಿಪ್ಗಳ ವಿದ್ಯುತ್ ಕಾರ್ಯಕ್ಷಮತೆಯು ಮಾನದಂಡಗಳನ್ನು ಪೂರೈಸುತ್ತದೆ ಎಂದು ಖಚಿತಪಡಿಸಿಕೊಳ್ಳಿ, ನಂತರದ ಅನ್ವಯಿಕೆಗಳಲ್ಲಿ ವಿಶ್ವಾಸಾರ್ಹತೆಯನ್ನು ಖಾತರಿಪಡಿಸುತ್ತದೆ. |
ವಿಂಗಡಣೆ ಹಂತ | - ಟೇಪ್ ಫ್ರೇಮ್ನಿಂದ ಅರ್ಹ ಚಿಪ್ಗಳನ್ನು ಬೇರ್ಪಡಿಸಲು ರೋಬೋಟಿಕ್ ಆರ್ಮ್ಗಳು ಅಥವಾ ವ್ಯಾಕ್ಯೂಮ್ ಸಕ್ಷನ್ ಕಪ್ಗಳನ್ನು ಬಳಸಿ ಮತ್ತು ಕಾರ್ಯಕ್ಷಮತೆಯ ಆಧಾರದ ಮೇಲೆ ಅವುಗಳನ್ನು ಸ್ವಯಂಚಾಲಿತವಾಗಿ ವಿಂಗಡಿಸಿ, ನಿಖರತೆಯನ್ನು ಸುಧಾರಿಸುವಾಗ ಉತ್ಪಾದನಾ ದಕ್ಷತೆ ಮತ್ತು ನಮ್ಯತೆಯನ್ನು ಖಚಿತಪಡಿಸುತ್ತದೆ. |
ವೇಫರ್ ಕತ್ತರಿಸುವ ಪ್ರಕ್ರಿಯೆಯು ವೇಫರ್ ಶುಚಿಗೊಳಿಸುವಿಕೆ, ಸ್ಥಾನೀಕರಣ, ಕತ್ತರಿಸುವುದು, ಶುಚಿಗೊಳಿಸುವಿಕೆ, ತಪಾಸಣೆ ಮತ್ತು ವಿಂಗಡಣೆಯನ್ನು ಒಳಗೊಂಡಿರುತ್ತದೆ, ಪ್ರತಿ ಹಂತವೂ ನಿರ್ಣಾಯಕವಾಗಿರುತ್ತದೆ. ಯಾಂತ್ರೀಕೃತಗೊಂಡ, ಲೇಸರ್ ಕತ್ತರಿಸುವಿಕೆ ಮತ್ತು AI ತಪಾಸಣೆ ತಂತ್ರಜ್ಞಾನಗಳಲ್ಲಿನ ಪ್ರಗತಿಯೊಂದಿಗೆ, ಆಧುನಿಕ ವೇಫರ್ ಕತ್ತರಿಸುವ ವ್ಯವಸ್ಥೆಗಳು ಹೆಚ್ಚಿನ ನಿಖರತೆ, ವೇಗ ಮತ್ತು ಕಡಿಮೆ ವಸ್ತು ನಷ್ಟವನ್ನು ಸಾಧಿಸಬಹುದು. ಭವಿಷ್ಯದಲ್ಲಿ, ಲೇಸರ್ ಮತ್ತು ಪ್ಲಾಸ್ಮಾದಂತಹ ಹೊಸ ಕತ್ತರಿಸುವ ತಂತ್ರಜ್ಞಾನಗಳು ಕ್ರಮೇಣ ಸಾಂಪ್ರದಾಯಿಕ ಬ್ಲೇಡ್ ಕತ್ತರಿಸುವಿಕೆಯನ್ನು ಬದಲಾಯಿಸುತ್ತವೆ, ಇದು ಹೆಚ್ಚು ಸಂಕೀರ್ಣವಾದ ಚಿಪ್ ವಿನ್ಯಾಸಗಳ ಅಗತ್ಯಗಳನ್ನು ಪೂರೈಸುತ್ತದೆ, ಅರೆವಾಹಕ ಉತ್ಪಾದನಾ ಪ್ರಕ್ರಿಯೆಗಳ ಅಭಿವೃದ್ಧಿಯನ್ನು ಮತ್ತಷ್ಟು ಹೆಚ್ಚಿಸುತ್ತದೆ.
ವೇಫರ್ ಕತ್ತರಿಸುವ ತಂತ್ರಜ್ಞಾನ ಮತ್ತು ಅದರ ತತ್ವಗಳು
ಚಿತ್ರವು ಮೂರು ಸಾಮಾನ್ಯ ವೇಫರ್ ಕತ್ತರಿಸುವ ತಂತ್ರಜ್ಞಾನಗಳನ್ನು ವಿವರಿಸುತ್ತದೆ:ಬ್ಲೇಡ್ ಡೈಸಿಂಗ್,ಲೇಸರ್ ಡೈಸಿಂಗ್, ಮತ್ತುಪ್ಲಾಸ್ಮಾ ಡೈಸಿಂಗ್ಈ ಮೂರು ತಂತ್ರಗಳ ವಿವರವಾದ ವಿಶ್ಲೇಷಣೆ ಮತ್ತು ಪೂರಕ ವಿವರಣೆಯನ್ನು ಕೆಳಗೆ ನೀಡಲಾಗಿದೆ:
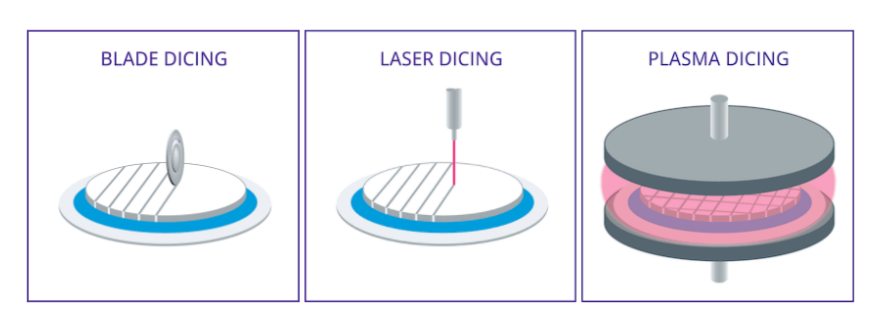
ಅರೆವಾಹಕ ತಯಾರಿಕೆಯಲ್ಲಿ, ವೇಫರ್ ಕತ್ತರಿಸುವುದು ಒಂದು ನಿರ್ಣಾಯಕ ಹಂತವಾಗಿದ್ದು, ವೇಫರ್ನ ದಪ್ಪವನ್ನು ಆಧರಿಸಿ ಸೂಕ್ತವಾದ ಕತ್ತರಿಸುವ ವಿಧಾನವನ್ನು ಆಯ್ಕೆ ಮಾಡಬೇಕಾಗುತ್ತದೆ. ಮೊದಲ ಹಂತವೆಂದರೆ ವೇಫರ್ನ ದಪ್ಪವನ್ನು ನಿರ್ಧರಿಸುವುದು. ವೇಫರ್ ದಪ್ಪವು 100 ಮೈಕ್ರಾನ್ಗಳನ್ನು ಮೀರಿದರೆ, ಬ್ಲೇಡ್ ಡೈಸಿಂಗ್ ಅನ್ನು ಕತ್ತರಿಸುವ ವಿಧಾನವಾಗಿ ಆಯ್ಕೆ ಮಾಡಬಹುದು. ಬ್ಲೇಡ್ ಡೈಸಿಂಗ್ ಸೂಕ್ತವಲ್ಲದಿದ್ದರೆ, ಫ್ರಾಕ್ಚರ್ ಡೈಸಿಂಗ್ ವಿಧಾನವನ್ನು ಬಳಸಬಹುದು, ಇದರಲ್ಲಿ ಸ್ಕ್ರೈಬ್ ಕಟಿಂಗ್ ಮತ್ತು ಬ್ಲೇಡ್ ಡೈಸಿಂಗ್ ತಂತ್ರಗಳು ಸೇರಿವೆ.
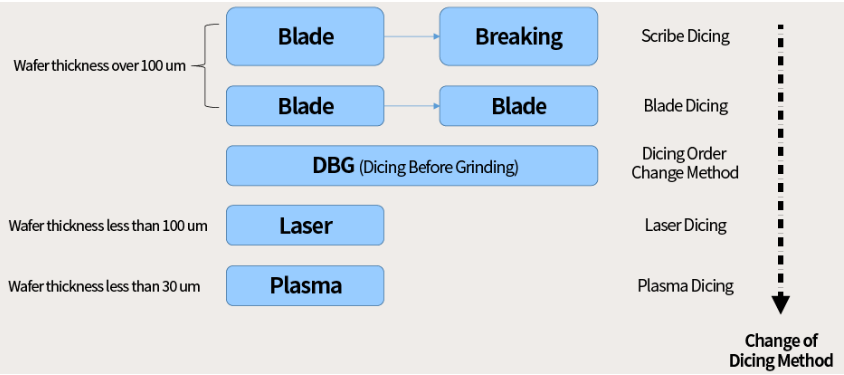
ವೇಫರ್ ದಪ್ಪವು 30 ರಿಂದ 100 ಮೈಕ್ರಾನ್ಗಳ ನಡುವೆ ಇದ್ದಾಗ, DBG (ಡೈಸ್ ಬಿಫೋರ್ ಗ್ರೈಂಡಿಂಗ್) ವಿಧಾನವನ್ನು ಶಿಫಾರಸು ಮಾಡಲಾಗುತ್ತದೆ. ಈ ಸಂದರ್ಭದಲ್ಲಿ, ಸ್ಕ್ರೈಬ್ ಕಟಿಂಗ್, ಬ್ಲೇಡ್ ಡೈಸಿಂಗ್ ಅಥವಾ ಅಗತ್ಯವಿರುವಂತೆ ಕತ್ತರಿಸುವ ಅನುಕ್ರಮವನ್ನು ಹೊಂದಿಸುವುದನ್ನು ಆಯ್ಕೆ ಮಾಡಬಹುದು, ಇದರಿಂದಾಗಿ ಉತ್ತಮ ಫಲಿತಾಂಶಗಳನ್ನು ಸಾಧಿಸಬಹುದು.
30 ಮೈಕ್ರಾನ್ಗಳಿಗಿಂತ ಕಡಿಮೆ ದಪ್ಪವಿರುವ ಅತಿ-ತೆಳುವಾದ ವೇಫರ್ಗಳಿಗೆ, ಹೆಚ್ಚಿನ ಹಾನಿಯನ್ನುಂಟುಮಾಡದೆ ತೆಳುವಾದ ವೇಫರ್ಗಳನ್ನು ನಿಖರವಾಗಿ ಕತ್ತರಿಸುವ ಸಾಮರ್ಥ್ಯದಿಂದಾಗಿ ಲೇಸರ್ ಕತ್ತರಿಸುವುದು ಆದ್ಯತೆಯ ವಿಧಾನವಾಗಿದೆ. ಲೇಸರ್ ಕತ್ತರಿಸುವುದು ನಿರ್ದಿಷ್ಟ ಅವಶ್ಯಕತೆಗಳನ್ನು ಪೂರೈಸಲು ಸಾಧ್ಯವಾಗದಿದ್ದರೆ, ಪ್ಲಾಸ್ಮಾ ಕತ್ತರಿಸುವಿಕೆಯನ್ನು ಪರ್ಯಾಯವಾಗಿ ಬಳಸಬಹುದು. ವಿಭಿನ್ನ ದಪ್ಪದ ಪರಿಸ್ಥಿತಿಗಳಲ್ಲಿ ಹೆಚ್ಚು ಸೂಕ್ತವಾದ ವೇಫರ್ ಕತ್ತರಿಸುವ ತಂತ್ರಜ್ಞಾನವನ್ನು ಆಯ್ಕೆ ಮಾಡಲಾಗಿದೆಯೆ ಎಂದು ಖಚಿತಪಡಿಸಿಕೊಳ್ಳಲು ಈ ಫ್ಲೋಚಾರ್ಟ್ ಸ್ಪಷ್ಟ ನಿರ್ಧಾರ ತೆಗೆದುಕೊಳ್ಳುವ ಮಾರ್ಗವನ್ನು ಒದಗಿಸುತ್ತದೆ.
2.1 ಯಾಂತ್ರಿಕ ಕತ್ತರಿಸುವ ತಂತ್ರಜ್ಞಾನ
ಯಾಂತ್ರಿಕ ಕತ್ತರಿಸುವ ತಂತ್ರಜ್ಞಾನವು ವೇಫರ್ ಡೈಸಿಂಗ್ನಲ್ಲಿ ಸಾಂಪ್ರದಾಯಿಕ ವಿಧಾನವಾಗಿದೆ. ವೇಫರ್ ಅನ್ನು ಕತ್ತರಿಸಲು ಕತ್ತರಿಸುವ ಸಾಧನವಾಗಿ ಹೆಚ್ಚಿನ ವೇಗದ ತಿರುಗುವ ವಜ್ರ ಗ್ರೈಂಡಿಂಗ್ ಚಕ್ರವನ್ನು ಬಳಸುವುದು ಮೂಲ ತತ್ವವಾಗಿದೆ. ಪ್ರಮುಖ ಉಪಕರಣಗಳು ಗಾಳಿ-ಬೇರಿಂಗ್ ಸ್ಪಿಂಡಲ್ ಅನ್ನು ಒಳಗೊಂಡಿರುತ್ತವೆ, ಇದು ಪೂರ್ವನಿರ್ಧರಿತ ಕತ್ತರಿಸುವ ಮಾರ್ಗದಲ್ಲಿ ನಿಖರವಾದ ಕತ್ತರಿಸುವುದು ಅಥವಾ ಗ್ರೂವಿಂಗ್ ಅನ್ನು ನಿರ್ವಹಿಸಲು ವಜ್ರ ಗ್ರೈಂಡಿಂಗ್ ಚಕ್ರ ಉಪಕರಣವನ್ನು ಹೆಚ್ಚಿನ ವೇಗದಲ್ಲಿ ಚಾಲನೆ ಮಾಡುತ್ತದೆ. ಈ ತಂತ್ರಜ್ಞಾನವನ್ನು ಅದರ ಕಡಿಮೆ ವೆಚ್ಚ, ಹೆಚ್ಚಿನ ದಕ್ಷತೆ ಮತ್ತು ವಿಶಾಲ ಅನ್ವಯಿಕತೆಯಿಂದಾಗಿ ಉದ್ಯಮದಲ್ಲಿ ವ್ಯಾಪಕವಾಗಿ ಬಳಸಲಾಗುತ್ತದೆ.
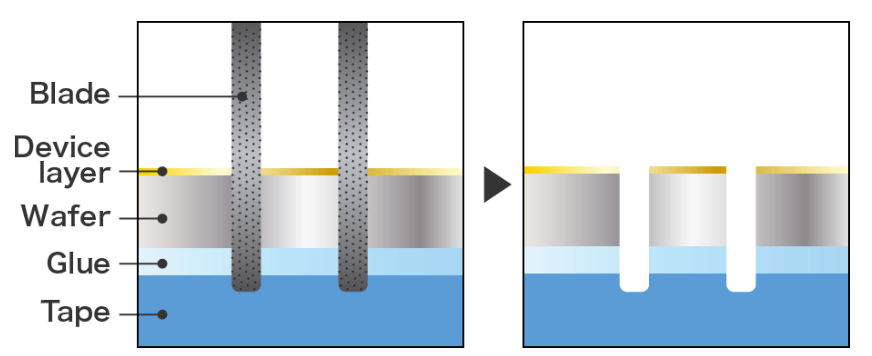
ಅನುಕೂಲಗಳು
ವಜ್ರದ ಗ್ರೈಂಡಿಂಗ್ ವೀಲ್ ಉಪಕರಣಗಳ ಹೆಚ್ಚಿನ ಗಡಸುತನ ಮತ್ತು ಉಡುಗೆ ಪ್ರತಿರೋಧವು ಯಾಂತ್ರಿಕ ಕತ್ತರಿಸುವ ತಂತ್ರಜ್ಞಾನವನ್ನು ವಿವಿಧ ವೇಫರ್ ವಸ್ತುಗಳ ಕತ್ತರಿಸುವ ಅಗತ್ಯಗಳಿಗೆ ಹೊಂದಿಕೊಳ್ಳಲು ಅನುವು ಮಾಡಿಕೊಡುತ್ತದೆ, ಅದು ಸಾಂಪ್ರದಾಯಿಕ ಸಿಲಿಕಾನ್-ಆಧಾರಿತ ವಸ್ತುಗಳು ಅಥವಾ ಹೊಸ ಸಂಯುಕ್ತ ಅರೆವಾಹಕಗಳಾಗಿರಬಹುದು. ಇದರ ಕಾರ್ಯಾಚರಣೆಯು ಸರಳವಾಗಿದೆ, ತುಲನಾತ್ಮಕವಾಗಿ ಕಡಿಮೆ ತಾಂತ್ರಿಕ ಅವಶ್ಯಕತೆಗಳೊಂದಿಗೆ, ಸಾಮೂಹಿಕ ಉತ್ಪಾದನೆಯಲ್ಲಿ ಅದರ ಜನಪ್ರಿಯತೆಯನ್ನು ಮತ್ತಷ್ಟು ಉತ್ತೇಜಿಸುತ್ತದೆ. ಹೆಚ್ಚುವರಿಯಾಗಿ, ಲೇಸರ್ ಕತ್ತರಿಸುವಂತಹ ಇತರ ಕತ್ತರಿಸುವ ವಿಧಾನಗಳಿಗೆ ಹೋಲಿಸಿದರೆ, ಯಾಂತ್ರಿಕ ಕತ್ತರಿಸುವುದು ಹೆಚ್ಚು ನಿಯಂತ್ರಿಸಬಹುದಾದ ವೆಚ್ಚವನ್ನು ಹೊಂದಿದೆ, ಇದು ಹೆಚ್ಚಿನ ಪ್ರಮಾಣದ ಉತ್ಪಾದನಾ ಅಗತ್ಯಗಳಿಗೆ ಸೂಕ್ತವಾಗಿದೆ.
ಮಿತಿಗಳು
ಅದರ ಹಲವಾರು ಅನುಕೂಲಗಳ ಹೊರತಾಗಿಯೂ, ಯಾಂತ್ರಿಕ ಕತ್ತರಿಸುವ ತಂತ್ರಜ್ಞಾನವು ಮಿತಿಗಳನ್ನು ಹೊಂದಿದೆ. ಮೊದಲನೆಯದಾಗಿ, ಉಪಕರಣ ಮತ್ತು ವೇಫರ್ ನಡುವಿನ ಭೌತಿಕ ಸಂಪರ್ಕದಿಂದಾಗಿ, ಕತ್ತರಿಸುವ ನಿಖರತೆಯು ತುಲನಾತ್ಮಕವಾಗಿ ಸೀಮಿತವಾಗಿರುತ್ತದೆ, ಇದು ನಂತರದ ಚಿಪ್ ಪ್ಯಾಕೇಜಿಂಗ್ ಮತ್ತು ಪರೀಕ್ಷೆಯ ನಿಖರತೆಯ ಮೇಲೆ ಪರಿಣಾಮ ಬೀರುವ ಆಯಾಮದ ವಿಚಲನಗಳಿಗೆ ಕಾರಣವಾಗುತ್ತದೆ. ಎರಡನೆಯದಾಗಿ, ಯಾಂತ್ರಿಕ ಕತ್ತರಿಸುವ ಪ್ರಕ್ರಿಯೆಯಲ್ಲಿ ಚಿಪ್ಪಿಂಗ್ ಮತ್ತು ಬಿರುಕುಗಳಂತಹ ದೋಷಗಳು ಸುಲಭವಾಗಿ ಸಂಭವಿಸಬಹುದು, ಇದು ಇಳುವರಿ ದರದ ಮೇಲೆ ಪರಿಣಾಮ ಬೀರುವುದಲ್ಲದೆ, ಚಿಪ್ಗಳ ವಿಶ್ವಾಸಾರ್ಹತೆ ಮತ್ತು ಜೀವಿತಾವಧಿಯ ಮೇಲೆ ನಕಾರಾತ್ಮಕ ಪರಿಣಾಮ ಬೀರುತ್ತದೆ. ಯಾಂತ್ರಿಕ ಒತ್ತಡದಿಂದ ಉಂಟಾಗುವ ಹಾನಿಯು ಹೆಚ್ಚಿನ ಸಾಂದ್ರತೆಯ ಚಿಪ್ ತಯಾರಿಕೆಗೆ ವಿಶೇಷವಾಗಿ ಹಾನಿಕಾರಕವಾಗಿದೆ, ವಿಶೇಷವಾಗಿ ಈ ಸಮಸ್ಯೆಗಳು ಹೆಚ್ಚು ಪ್ರಮುಖವಾಗಿರುವ ದುರ್ಬಲವಾದ ವಸ್ತುಗಳನ್ನು ಕತ್ತರಿಸುವಾಗ.
ತಾಂತ್ರಿಕ ಸುಧಾರಣೆಗಳು
ಈ ಮಿತಿಗಳನ್ನು ನಿವಾರಿಸಲು, ಸಂಶೋಧಕರು ನಿರಂತರವಾಗಿ ಯಾಂತ್ರಿಕ ಕತ್ತರಿಸುವ ಪ್ರಕ್ರಿಯೆಯನ್ನು ಅತ್ಯುತ್ತಮವಾಗಿಸುತ್ತಿದ್ದಾರೆ. ಪ್ರಮುಖ ಸುಧಾರಣೆಗಳಲ್ಲಿ ಕತ್ತರಿಸುವ ನಿಖರತೆ ಮತ್ತು ಬಾಳಿಕೆಯನ್ನು ಸುಧಾರಿಸಲು ಗ್ರೈಂಡಿಂಗ್ ಚಕ್ರಗಳ ವಿನ್ಯಾಸ ಮತ್ತು ವಸ್ತುಗಳ ಆಯ್ಕೆಯನ್ನು ಹೆಚ್ಚಿಸುವುದು ಸೇರಿದೆ. ಹೆಚ್ಚುವರಿಯಾಗಿ, ಕತ್ತರಿಸುವ ಉಪಕರಣಗಳ ರಚನಾತ್ಮಕ ವಿನ್ಯಾಸ ಮತ್ತು ನಿಯಂತ್ರಣ ವ್ಯವಸ್ಥೆಗಳನ್ನು ಅತ್ಯುತ್ತಮವಾಗಿಸುವುದರಿಂದ ಕತ್ತರಿಸುವ ಪ್ರಕ್ರಿಯೆಯ ಸ್ಥಿರತೆ ಮತ್ತು ಯಾಂತ್ರೀಕರಣವು ಮತ್ತಷ್ಟು ಸುಧಾರಿಸಿದೆ. ಈ ಪ್ರಗತಿಗಳು ಮಾನವ ಕಾರ್ಯಾಚರಣೆಗಳಿಂದ ಉಂಟಾಗುವ ದೋಷಗಳನ್ನು ಕಡಿಮೆ ಮಾಡುತ್ತದೆ ಮತ್ತು ಕಡಿತಗಳ ಸ್ಥಿರತೆಯನ್ನು ಸುಧಾರಿಸುತ್ತದೆ. ಕತ್ತರಿಸುವ ಪ್ರಕ್ರಿಯೆಯ ಸಮಯದಲ್ಲಿ ವೈಪರೀತ್ಯಗಳ ನೈಜ-ಸಮಯದ ಮೇಲ್ವಿಚಾರಣೆಗಾಗಿ ಸುಧಾರಿತ ತಪಾಸಣೆ ಮತ್ತು ಗುಣಮಟ್ಟ ನಿಯಂತ್ರಣ ತಂತ್ರಜ್ಞಾನಗಳ ಪರಿಚಯವು ಕತ್ತರಿಸುವ ವಿಶ್ವಾಸಾರ್ಹತೆ ಮತ್ತು ಇಳುವರಿಯನ್ನು ಗಮನಾರ್ಹವಾಗಿ ಸುಧಾರಿಸಿದೆ.
ಭವಿಷ್ಯದ ಅಭಿವೃದ್ಧಿ ಮತ್ತು ಹೊಸ ತಂತ್ರಜ್ಞಾನಗಳು
ವೇಫರ್ ಕತ್ತರಿಸುವಲ್ಲಿ ಯಾಂತ್ರಿಕ ಕತ್ತರಿಸುವ ತಂತ್ರಜ್ಞಾನವು ಇನ್ನೂ ಮಹತ್ವದ ಸ್ಥಾನವನ್ನು ಹೊಂದಿದ್ದರೂ, ಅರೆವಾಹಕ ಪ್ರಕ್ರಿಯೆಗಳು ವಿಕಸನಗೊಳ್ಳುತ್ತಿದ್ದಂತೆ ಹೊಸ ಕತ್ತರಿಸುವ ತಂತ್ರಜ್ಞಾನಗಳು ವೇಗವಾಗಿ ಮುಂದುವರಿಯುತ್ತಿವೆ. ಉದಾಹರಣೆಗೆ, ಥರ್ಮಲ್ ಲೇಸರ್ ಕತ್ತರಿಸುವ ತಂತ್ರಜ್ಞಾನದ ಅನ್ವಯವು ಯಾಂತ್ರಿಕ ಕತ್ತರಿಸುವಿಕೆಯಲ್ಲಿನ ನಿಖರತೆ ಮತ್ತು ದೋಷದ ಸಮಸ್ಯೆಗಳಿಗೆ ಹೊಸ ಪರಿಹಾರಗಳನ್ನು ಒದಗಿಸುತ್ತದೆ. ಈ ಸಂಪರ್ಕವಿಲ್ಲದ ಕತ್ತರಿಸುವ ವಿಧಾನವು ವೇಫರ್ ಮೇಲಿನ ಭೌತಿಕ ಒತ್ತಡವನ್ನು ಕಡಿಮೆ ಮಾಡುತ್ತದೆ, ವಿಶೇಷವಾಗಿ ಹೆಚ್ಚು ದುರ್ಬಲವಾದ ವಸ್ತುಗಳನ್ನು ಕತ್ತರಿಸುವಾಗ ಚಿಪ್ಪಿಂಗ್ ಮತ್ತು ಬಿರುಕು ಬಿಡುವ ಸಂಭವವನ್ನು ಗಮನಾರ್ಹವಾಗಿ ಕಡಿಮೆ ಮಾಡುತ್ತದೆ. ಭವಿಷ್ಯದಲ್ಲಿ, ಉದಯೋನ್ಮುಖ ಕತ್ತರಿಸುವ ತಂತ್ರಗಳೊಂದಿಗೆ ಯಾಂತ್ರಿಕ ಕತ್ತರಿಸುವ ತಂತ್ರಜ್ಞಾನದ ಏಕೀಕರಣವು ಅರೆವಾಹಕ ಉತ್ಪಾದನೆಗೆ ಹೆಚ್ಚಿನ ಆಯ್ಕೆಗಳು ಮತ್ತು ನಮ್ಯತೆಯನ್ನು ಒದಗಿಸುತ್ತದೆ, ಉತ್ಪಾದನಾ ದಕ್ಷತೆ ಮತ್ತು ಚಿಪ್ ಗುಣಮಟ್ಟವನ್ನು ಮತ್ತಷ್ಟು ಹೆಚ್ಚಿಸುತ್ತದೆ.
ಕೊನೆಯಲ್ಲಿ, ಯಾಂತ್ರಿಕ ಕತ್ತರಿಸುವ ತಂತ್ರಜ್ಞಾನವು ಕೆಲವು ನ್ಯೂನತೆಗಳನ್ನು ಹೊಂದಿದ್ದರೂ, ನಿರಂತರ ತಾಂತ್ರಿಕ ಸುಧಾರಣೆಗಳು ಮತ್ತು ಹೊಸ ಕತ್ತರಿಸುವ ತಂತ್ರಗಳೊಂದಿಗೆ ಅದರ ಏಕೀಕರಣವು ಅರೆವಾಹಕ ಉತ್ಪಾದನೆಯಲ್ಲಿ ಇನ್ನೂ ಪ್ರಮುಖ ಪಾತ್ರವನ್ನು ವಹಿಸಲು ಮತ್ತು ಭವಿಷ್ಯದ ಪ್ರಕ್ರಿಯೆಗಳಲ್ಲಿ ಅದರ ಸ್ಪರ್ಧಾತ್ಮಕತೆಯನ್ನು ಕಾಪಾಡಿಕೊಳ್ಳಲು ಅನುವು ಮಾಡಿಕೊಡುತ್ತದೆ.
2.2 ಲೇಸರ್ ಕತ್ತರಿಸುವ ತಂತ್ರಜ್ಞಾನ
ವೇಫರ್ ಕತ್ತರಿಸುವಲ್ಲಿ ಹೊಸ ವಿಧಾನವಾಗಿ ಲೇಸರ್ ಕತ್ತರಿಸುವ ತಂತ್ರಜ್ಞಾನವು ಕ್ರಮೇಣ ಅರೆವಾಹಕ ಉದ್ಯಮದಲ್ಲಿ ವ್ಯಾಪಕ ಗಮನವನ್ನು ಗಳಿಸಿದೆ, ಏಕೆಂದರೆ ಅದರ ಹೆಚ್ಚಿನ ನಿಖರತೆ, ಯಾಂತ್ರಿಕ ಸಂಪರ್ಕ ಹಾನಿಯ ಕೊರತೆ ಮತ್ತು ತ್ವರಿತ ಕತ್ತರಿಸುವ ಸಾಮರ್ಥ್ಯಗಳು ಇದಕ್ಕೆ ಕಾರಣ. ಈ ತಂತ್ರಜ್ಞಾನವು ಲೇಸರ್ ಕಿರಣದ ಹೆಚ್ಚಿನ ಶಕ್ತಿ ಸಾಂದ್ರತೆ ಮತ್ತು ಕೇಂದ್ರೀಕರಿಸುವ ಸಾಮರ್ಥ್ಯವನ್ನು ಬಳಸಿಕೊಂಡು ವೇಫರ್ ವಸ್ತುವಿನ ಮೇಲ್ಮೈಯಲ್ಲಿ ಸಣ್ಣ ಶಾಖ-ಪೀಡಿತ ವಲಯವನ್ನು ಸೃಷ್ಟಿಸುತ್ತದೆ. ಲೇಸರ್ ಕಿರಣವನ್ನು ವೇಫರ್ಗೆ ಅನ್ವಯಿಸಿದಾಗ, ಉತ್ಪತ್ತಿಯಾಗುವ ಉಷ್ಣ ಒತ್ತಡವು ವಸ್ತುವು ಗೊತ್ತುಪಡಿಸಿದ ಸ್ಥಳದಲ್ಲಿ ಮುರಿತಕ್ಕೆ ಕಾರಣವಾಗುತ್ತದೆ, ನಿಖರವಾದ ಕತ್ತರಿಸುವಿಕೆಯನ್ನು ಸಾಧಿಸುತ್ತದೆ.
ಲೇಸರ್ ಕತ್ತರಿಸುವ ತಂತ್ರಜ್ಞಾನದ ಅನುಕೂಲಗಳು
• ಹೆಚ್ಚಿನ ನಿಖರತೆ: ಲೇಸರ್ ಕಿರಣದ ನಿಖರವಾದ ಸ್ಥಾನೀಕರಣ ಸಾಮರ್ಥ್ಯವು ಮೈಕ್ರಾನ್ ಅಥವಾ ನ್ಯಾನೊಮೀಟರ್-ಮಟ್ಟದ ಕತ್ತರಿಸುವ ನಿಖರತೆಯನ್ನು ಅನುಮತಿಸುತ್ತದೆ, ಆಧುನಿಕ ಹೆಚ್ಚಿನ ನಿಖರತೆ, ಹೆಚ್ಚಿನ ಸಾಂದ್ರತೆಯ ಇಂಟಿಗ್ರೇಟೆಡ್ ಸರ್ಕ್ಯೂಟ್ ತಯಾರಿಕೆಯ ಅವಶ್ಯಕತೆಗಳನ್ನು ಪೂರೈಸುತ್ತದೆ.
• ಯಾಂತ್ರಿಕ ಸಂಪರ್ಕವಿಲ್ಲ: ಲೇಸರ್ ಕತ್ತರಿಸುವಿಕೆಯು ವೇಫರ್ನೊಂದಿಗಿನ ಭೌತಿಕ ಸಂಪರ್ಕವನ್ನು ತಪ್ಪಿಸುತ್ತದೆ, ಚಿಪ್ಪಿಂಗ್ ಮತ್ತು ಕ್ರ್ಯಾಕಿಂಗ್ನಂತಹ ಯಾಂತ್ರಿಕ ಕತ್ತರಿಸುವಿಕೆಯಲ್ಲಿ ಸಾಮಾನ್ಯ ಸಮಸ್ಯೆಗಳನ್ನು ತಡೆಯುತ್ತದೆ, ಚಿಪ್ಗಳ ಇಳುವರಿ ದರ ಮತ್ತು ವಿಶ್ವಾಸಾರ್ಹತೆಯನ್ನು ಗಮನಾರ್ಹವಾಗಿ ಸುಧಾರಿಸುತ್ತದೆ.
• ವೇಗದ ಕತ್ತರಿಸುವ ವೇಗ: ಲೇಸರ್ ಕತ್ತರಿಸುವಿಕೆಯ ಹೆಚ್ಚಿನ ವೇಗವು ಉತ್ಪಾದನಾ ದಕ್ಷತೆಯನ್ನು ಹೆಚ್ಚಿಸಲು ಕೊಡುಗೆ ನೀಡುತ್ತದೆ, ಇದು ವಿಶೇಷವಾಗಿ ದೊಡ್ಡ-ಪ್ರಮಾಣದ, ಹೆಚ್ಚಿನ-ವೇಗದ ಉತ್ಪಾದನಾ ಸನ್ನಿವೇಶಗಳಿಗೆ ಸೂಕ್ತವಾಗಿದೆ.
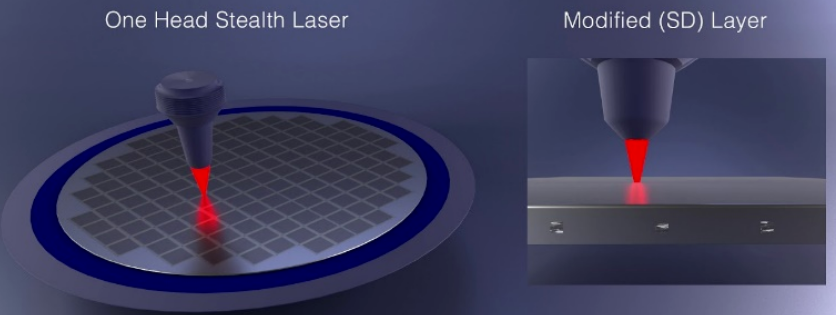
ಎದುರಿಸಿದ ಸವಾಲುಗಳು
• ಹೆಚ್ಚಿನ ಸಲಕರಣೆಗಳ ವೆಚ್ಚ: ಲೇಸರ್ ಕತ್ತರಿಸುವ ಉಪಕರಣಗಳಿಗೆ ಆರಂಭಿಕ ಹೂಡಿಕೆ ಹೆಚ್ಚಾಗಿರುತ್ತದೆ, ಇದು ಆರ್ಥಿಕ ಒತ್ತಡವನ್ನು ಒದಗಿಸುತ್ತದೆ, ವಿಶೇಷವಾಗಿ ಸಣ್ಣ ಮತ್ತು ಮಧ್ಯಮ ಗಾತ್ರದ ಉತ್ಪಾದನಾ ಉದ್ಯಮಗಳಿಗೆ.
• ಸಂಕೀರ್ಣ ಪ್ರಕ್ರಿಯೆ ನಿಯಂತ್ರಣ: ಲೇಸರ್ ಕತ್ತರಿಸುವಿಕೆಗೆ ಶಕ್ತಿಯ ಸಾಂದ್ರತೆ, ಗಮನ ಸ್ಥಾನ ಮತ್ತು ಕತ್ತರಿಸುವ ವೇಗ ಸೇರಿದಂತೆ ಹಲವಾರು ನಿಯತಾಂಕಗಳ ನಿಖರವಾದ ನಿಯಂತ್ರಣದ ಅಗತ್ಯವಿರುತ್ತದೆ, ಇದು ಪ್ರಕ್ರಿಯೆಯನ್ನು ಸಂಕೀರ್ಣಗೊಳಿಸುತ್ತದೆ.
• ಶಾಖ-ಪೀಡಿತ ವಲಯ ಸಮಸ್ಯೆಗಳು: ಲೇಸರ್ ಕತ್ತರಿಸುವಿಕೆಯ ಸಂಪರ್ಕವಿಲ್ಲದ ಸ್ವಭಾವವು ಯಾಂತ್ರಿಕ ಹಾನಿಯನ್ನು ಕಡಿಮೆ ಮಾಡುತ್ತದೆಯಾದರೂ, ಶಾಖ-ಪೀಡಿತ ವಲಯದಿಂದ (HAZ) ಉಂಟಾಗುವ ಉಷ್ಣ ಒತ್ತಡವು ವೇಫರ್ ವಸ್ತುವಿನ ಗುಣಲಕ್ಷಣಗಳ ಮೇಲೆ ನಕಾರಾತ್ಮಕ ಪರಿಣಾಮ ಬೀರುತ್ತದೆ. ಈ ಪರಿಣಾಮವನ್ನು ಕಡಿಮೆ ಮಾಡಲು ಪ್ರಕ್ರಿಯೆಯ ಮತ್ತಷ್ಟು ಆಪ್ಟಿಮೈಸೇಶನ್ ಅಗತ್ಯವಿದೆ.
ತಾಂತ್ರಿಕ ಸುಧಾರಣಾ ನಿರ್ದೇಶನಗಳು
ಈ ಸವಾಲುಗಳನ್ನು ಎದುರಿಸಲು, ಸಂಶೋಧಕರು ಸಲಕರಣೆಗಳ ವೆಚ್ಚವನ್ನು ಕಡಿಮೆ ಮಾಡುವುದು, ಕಡಿತಗೊಳಿಸುವ ದಕ್ಷತೆಯನ್ನು ಸುಧಾರಿಸುವುದು ಮತ್ತು ಪ್ರಕ್ರಿಯೆಯ ಹರಿವನ್ನು ಉತ್ತಮಗೊಳಿಸುವತ್ತ ಗಮನ ಹರಿಸುತ್ತಿದ್ದಾರೆ.
• ದಕ್ಷ ಲೇಸರ್ಗಳು ಮತ್ತು ಆಪ್ಟಿಕಲ್ ವ್ಯವಸ್ಥೆಗಳು: ಹೆಚ್ಚು ಪರಿಣಾಮಕಾರಿ ಲೇಸರ್ಗಳು ಮತ್ತು ಸುಧಾರಿತ ಆಪ್ಟಿಕಲ್ ವ್ಯವಸ್ಥೆಗಳನ್ನು ಅಭಿವೃದ್ಧಿಪಡಿಸುವ ಮೂಲಕ, ಕತ್ತರಿಸುವ ನಿಖರತೆ ಮತ್ತು ವೇಗವನ್ನು ಹೆಚ್ಚಿಸುವಾಗ ಸಲಕರಣೆಗಳ ವೆಚ್ಚವನ್ನು ಕಡಿಮೆ ಮಾಡಲು ಸಾಧ್ಯವಿದೆ.
• ಪ್ರಕ್ರಿಯೆಯ ನಿಯತಾಂಕಗಳನ್ನು ಅತ್ಯುತ್ತಮವಾಗಿಸುವುದು: ಶಾಖ-ಪೀಡಿತ ವಲಯವನ್ನು ಕಡಿಮೆ ಮಾಡುವ ಪ್ರಕ್ರಿಯೆಗಳನ್ನು ಸುಧಾರಿಸಲು, ಇದರಿಂದಾಗಿ ಕತ್ತರಿಸುವ ಗುಣಮಟ್ಟವನ್ನು ಸುಧಾರಿಸಲು ಲೇಸರ್ಗಳು ಮತ್ತು ವೇಫರ್ ವಸ್ತುಗಳ ನಡುವಿನ ಪರಸ್ಪರ ಕ್ರಿಯೆಯ ಕುರಿತು ಆಳವಾದ ಸಂಶೋಧನೆಯನ್ನು ನಡೆಸಲಾಗುತ್ತಿದೆ.
• ಬುದ್ಧಿವಂತ ನಿಯಂತ್ರಣ ವ್ಯವಸ್ಥೆಗಳು: ಬುದ್ಧಿವಂತ ನಿಯಂತ್ರಣ ತಂತ್ರಜ್ಞಾನಗಳ ಅಭಿವೃದ್ಧಿಯು ಲೇಸರ್ ಕತ್ತರಿಸುವ ಪ್ರಕ್ರಿಯೆಯನ್ನು ಸ್ವಯಂಚಾಲಿತಗೊಳಿಸುವ ಮತ್ತು ಅತ್ಯುತ್ತಮವಾಗಿಸುವ ಗುರಿಯನ್ನು ಹೊಂದಿದೆ, ಅದರ ಸ್ಥಿರತೆ ಮತ್ತು ಸ್ಥಿರತೆಯನ್ನು ಸುಧಾರಿಸುತ್ತದೆ.
ಲೇಸರ್ ಕತ್ತರಿಸುವ ತಂತ್ರಜ್ಞಾನವು ಅತಿ ತೆಳುವಾದ ವೇಫರ್ಗಳು ಮತ್ತು ಹೆಚ್ಚಿನ-ನಿಖರ ಕತ್ತರಿಸುವ ಸನ್ನಿವೇಶಗಳಲ್ಲಿ ವಿಶೇಷವಾಗಿ ಪರಿಣಾಮಕಾರಿಯಾಗಿದೆ. ವೇಫರ್ ಗಾತ್ರಗಳು ಹೆಚ್ಚಾದಂತೆ ಮತ್ತು ಸರ್ಕ್ಯೂಟ್ ಸಾಂದ್ರತೆಗಳು ಹೆಚ್ಚಾದಂತೆ, ಸಾಂಪ್ರದಾಯಿಕ ಯಾಂತ್ರಿಕ ಕತ್ತರಿಸುವ ವಿಧಾನಗಳು ಆಧುನಿಕ ಅರೆವಾಹಕ ಉತ್ಪಾದನೆಯ ಹೆಚ್ಚಿನ-ನಿಖರತೆ ಮತ್ತು ಹೆಚ್ಚಿನ-ದಕ್ಷತೆಯ ಬೇಡಿಕೆಗಳನ್ನು ಪೂರೈಸಲು ಹೆಣಗಾಡುತ್ತವೆ. ಅದರ ವಿಶಿಷ್ಟ ಅನುಕೂಲಗಳಿಂದಾಗಿ, ಈ ಕ್ಷೇತ್ರಗಳಲ್ಲಿ ಲೇಸರ್ ಕತ್ತರಿಸುವುದು ಆದ್ಯತೆಯ ಪರಿಹಾರವಾಗುತ್ತಿದೆ.
ಲೇಸರ್ ಕತ್ತರಿಸುವ ತಂತ್ರಜ್ಞಾನವು ಇನ್ನೂ ಹೆಚ್ಚಿನ ಸಲಕರಣೆಗಳ ವೆಚ್ಚ ಮತ್ತು ಪ್ರಕ್ರಿಯೆಯ ಸಂಕೀರ್ಣತೆಯಂತಹ ಸವಾಲುಗಳನ್ನು ಎದುರಿಸುತ್ತಿದ್ದರೂ, ಹೆಚ್ಚಿನ ನಿಖರತೆ ಮತ್ತು ಸಂಪರ್ಕವಿಲ್ಲದ ಹಾನಿಯಲ್ಲಿ ಅದರ ವಿಶಿಷ್ಟ ಅನುಕೂಲಗಳು ಅರೆವಾಹಕ ತಯಾರಿಕೆಯಲ್ಲಿ ಅಭಿವೃದ್ಧಿಗೆ ಪ್ರಮುಖ ನಿರ್ದೇಶನವಾಗಿದೆ. ಲೇಸರ್ ತಂತ್ರಜ್ಞಾನ ಮತ್ತು ಬುದ್ಧಿವಂತ ನಿಯಂತ್ರಣ ವ್ಯವಸ್ಥೆಗಳು ಮುಂದುವರೆದಂತೆ, ಲೇಸರ್ ಕತ್ತರಿಸುವಿಕೆಯು ವೇಫರ್ ಕತ್ತರಿಸುವ ದಕ್ಷತೆ ಮತ್ತು ಗುಣಮಟ್ಟವನ್ನು ಮತ್ತಷ್ಟು ಸುಧಾರಿಸುತ್ತದೆ ಎಂದು ನಿರೀಕ್ಷಿಸಲಾಗಿದೆ, ಇದು ಅರೆವಾಹಕ ಉದ್ಯಮದ ನಿರಂತರ ಅಭಿವೃದ್ಧಿಗೆ ಚಾಲನೆ ನೀಡುತ್ತದೆ.
2.3 ಪ್ಲಾಸ್ಮಾ ಕತ್ತರಿಸುವ ತಂತ್ರಜ್ಞಾನ
ಪ್ಲಾಸ್ಮಾ ಕತ್ತರಿಸುವ ತಂತ್ರಜ್ಞಾನವು, ಉದಯೋನ್ಮುಖ ವೇಫರ್ ಡೈಸಿಂಗ್ ವಿಧಾನವಾಗಿ, ಇತ್ತೀಚಿನ ವರ್ಷಗಳಲ್ಲಿ ಗಮನಾರ್ಹ ಗಮನ ಸೆಳೆದಿದೆ. ಈ ತಂತ್ರಜ್ಞಾನವು ಪ್ಲಾಸ್ಮಾ ಕಿರಣದ ಶಕ್ತಿ, ವೇಗ ಮತ್ತು ಕತ್ತರಿಸುವ ಮಾರ್ಗವನ್ನು ನಿಯಂತ್ರಿಸುವ ಮೂಲಕ ವೇಫರ್ಗಳನ್ನು ನಿಖರವಾಗಿ ಕತ್ತರಿಸಲು ಹೆಚ್ಚಿನ ಶಕ್ತಿಯ ಪ್ಲಾಸ್ಮಾ ಕಿರಣಗಳನ್ನು ಬಳಸುತ್ತದೆ, ಅತ್ಯುತ್ತಮ ಕತ್ತರಿಸುವ ಫಲಿತಾಂಶಗಳನ್ನು ಸಾಧಿಸುತ್ತದೆ.
ಕೆಲಸದ ತತ್ವ ಮತ್ತು ಅನುಕೂಲಗಳು
ಪ್ಲಾಸ್ಮಾ ಕತ್ತರಿಸುವ ಪ್ರಕ್ರಿಯೆಯು ಉಪಕರಣದಿಂದ ಉತ್ಪತ್ತಿಯಾಗುವ ಹೆಚ್ಚಿನ-ತಾಪಮಾನದ, ಹೆಚ್ಚಿನ-ಶಕ್ತಿಯ ಪ್ಲಾಸ್ಮಾ ಕಿರಣವನ್ನು ಅವಲಂಬಿಸಿದೆ. ಈ ಕಿರಣವು ವೇಫರ್ ವಸ್ತುವನ್ನು ಅದರ ಕರಗುವ ಅಥವಾ ಆವಿಯಾಗುವ ಹಂತಕ್ಕೆ ಬಹಳ ಕಡಿಮೆ ಸಮಯದಲ್ಲಿ ಬಿಸಿ ಮಾಡಬಹುದು, ಇದು ವೇಗವಾಗಿ ಕತ್ತರಿಸಲು ಅನುವು ಮಾಡಿಕೊಡುತ್ತದೆ. ಸಾಂಪ್ರದಾಯಿಕ ಯಾಂತ್ರಿಕ ಅಥವಾ ಲೇಸರ್ ಕತ್ತರಿಸುವಿಕೆಗೆ ಹೋಲಿಸಿದರೆ, ಪ್ಲಾಸ್ಮಾ ಕತ್ತರಿಸುವುದು ವೇಗವಾಗಿರುತ್ತದೆ ಮತ್ತು ಸಣ್ಣ ಶಾಖ-ಪೀಡಿತ ವಲಯವನ್ನು ಉತ್ಪಾದಿಸುತ್ತದೆ, ಕತ್ತರಿಸುವ ಸಮಯದಲ್ಲಿ ಬಿರುಕುಗಳು ಮತ್ತು ಹಾನಿ ಸಂಭವಿಸುವುದನ್ನು ಪರಿಣಾಮಕಾರಿಯಾಗಿ ಕಡಿಮೆ ಮಾಡುತ್ತದೆ.
ಪ್ರಾಯೋಗಿಕ ಅನ್ವಯಿಕೆಗಳಲ್ಲಿ, ಪ್ಲಾಸ್ಮಾ ಕತ್ತರಿಸುವ ತಂತ್ರಜ್ಞಾನವು ಸಂಕೀರ್ಣ ಆಕಾರಗಳನ್ನು ಹೊಂದಿರುವ ವೇಫರ್ಗಳನ್ನು ನಿರ್ವಹಿಸುವಲ್ಲಿ ವಿಶೇಷವಾಗಿ ಪ್ರವೀಣವಾಗಿದೆ. ಇದರ ಹೆಚ್ಚಿನ ಶಕ್ತಿ, ಹೊಂದಾಣಿಕೆ ಮಾಡಬಹುದಾದ ಪ್ಲಾಸ್ಮಾ ಕಿರಣವು ಹೆಚ್ಚಿನ ನಿಖರತೆಯೊಂದಿಗೆ ಅನಿಯಮಿತ ಆಕಾರದ ವೇಫರ್ಗಳನ್ನು ಸುಲಭವಾಗಿ ಕತ್ತರಿಸಬಹುದು. ಆದ್ದರಿಂದ, ಮೈಕ್ರೋಎಲೆಕ್ಟ್ರಾನಿಕ್ಸ್ ತಯಾರಿಕೆಯಲ್ಲಿ, ವಿಶೇಷವಾಗಿ ಉನ್ನತ-ಮಟ್ಟದ ಚಿಪ್ಗಳ ಕಸ್ಟಮೈಸ್ ಮಾಡಿದ ಮತ್ತು ಸಣ್ಣ-ಬ್ಯಾಚ್ ಉತ್ಪಾದನೆಯಲ್ಲಿ, ಈ ತಂತ್ರಜ್ಞಾನವು ವ್ಯಾಪಕ ಬಳಕೆಗೆ ಉತ್ತಮ ಭರವಸೆಯನ್ನು ತೋರಿಸುತ್ತದೆ.
ಸವಾಲುಗಳು ಮತ್ತು ಮಿತಿಗಳು
ಪ್ಲಾಸ್ಮಾ ಕತ್ತರಿಸುವ ತಂತ್ರಜ್ಞಾನದ ಹಲವು ಅನುಕೂಲಗಳ ಹೊರತಾಗಿಯೂ, ಇದು ಕೆಲವು ಸವಾಲುಗಳನ್ನು ಎದುರಿಸುತ್ತಿದೆ.
• ಸಂಕೀರ್ಣ ಪ್ರಕ್ರಿಯೆ: ಪ್ಲಾಸ್ಮಾ ಕತ್ತರಿಸುವ ಪ್ರಕ್ರಿಯೆಯು ಸಂಕೀರ್ಣವಾಗಿದೆ ಮತ್ತು ಖಚಿತಪಡಿಸಿಕೊಳ್ಳಲು ಹೆಚ್ಚಿನ ನಿಖರತೆಯ ಉಪಕರಣಗಳು ಮತ್ತು ಅನುಭವಿ ನಿರ್ವಾಹಕರು ಅಗತ್ಯವಿದೆಕತ್ತರಿಸುವಲ್ಲಿ ನಿಖರತೆ ಮತ್ತು ಸ್ಥಿರತೆ.
• ಪರಿಸರ ನಿಯಂತ್ರಣ ಮತ್ತು ಸುರಕ್ಷತೆ: ಪ್ಲಾಸ್ಮಾ ಕಿರಣದ ಹೆಚ್ಚಿನ-ತಾಪಮಾನ, ಹೆಚ್ಚಿನ ಶಕ್ತಿಯ ಸ್ವಭಾವಕ್ಕೆ ಕಟ್ಟುನಿಟ್ಟಾದ ಪರಿಸರ ನಿಯಂತ್ರಣ ಮತ್ತು ಸುರಕ್ಷತಾ ಕ್ರಮಗಳು ಬೇಕಾಗುತ್ತವೆ, ಇದು ಅನುಷ್ಠಾನದ ಸಂಕೀರ್ಣತೆ ಮತ್ತು ವೆಚ್ಚವನ್ನು ಹೆಚ್ಚಿಸುತ್ತದೆ.
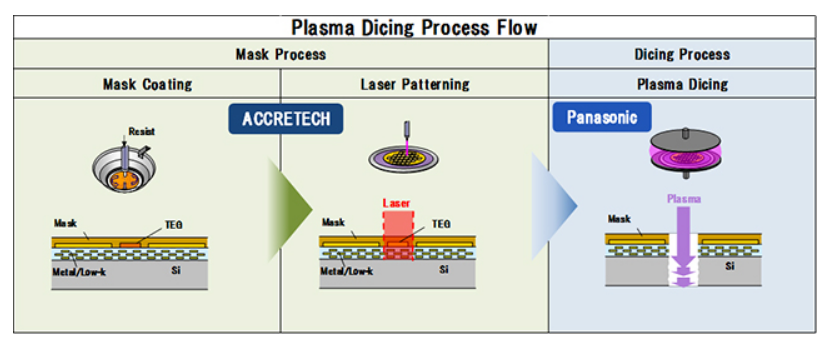
ಭವಿಷ್ಯದ ಅಭಿವೃದ್ಧಿ ನಿರ್ದೇಶನಗಳು
ತಾಂತ್ರಿಕ ಪ್ರಗತಿಯೊಂದಿಗೆ, ಪ್ಲಾಸ್ಮಾ ಕತ್ತರಿಸುವಿಕೆಗೆ ಸಂಬಂಧಿಸಿದ ಸವಾಲುಗಳನ್ನು ಕ್ರಮೇಣ ನಿವಾರಿಸುವ ನಿರೀಕ್ಷೆಯಿದೆ. ಚುರುಕಾದ ಮತ್ತು ಹೆಚ್ಚು ಸ್ಥಿರವಾದ ಕತ್ತರಿಸುವ ಉಪಕರಣಗಳನ್ನು ಅಭಿವೃದ್ಧಿಪಡಿಸುವ ಮೂಲಕ, ಹಸ್ತಚಾಲಿತ ಕಾರ್ಯಾಚರಣೆಗಳ ಮೇಲಿನ ಅವಲಂಬನೆಯನ್ನು ಕಡಿಮೆ ಮಾಡಬಹುದು, ಇದರಿಂದಾಗಿ ಉತ್ಪಾದನಾ ದಕ್ಷತೆಯನ್ನು ಸುಧಾರಿಸಬಹುದು. ಅದೇ ಸಮಯದಲ್ಲಿ, ಪ್ರಕ್ರಿಯೆಯ ನಿಯತಾಂಕಗಳು ಮತ್ತು ಕತ್ತರಿಸುವ ಪರಿಸರವನ್ನು ಅತ್ಯುತ್ತಮವಾಗಿಸುವುದರಿಂದ ಸುರಕ್ಷತಾ ಅಪಾಯಗಳು ಮತ್ತು ಕಾರ್ಯಾಚರಣೆಯ ವೆಚ್ಚಗಳನ್ನು ಕಡಿಮೆ ಮಾಡಲು ಸಹಾಯ ಮಾಡುತ್ತದೆ.
ಅರೆವಾಹಕ ಉದ್ಯಮದಲ್ಲಿ, ವೇಫರ್ ಕತ್ತರಿಸುವುದು ಮತ್ತು ಡೈಸಿಂಗ್ ತಂತ್ರಜ್ಞಾನದಲ್ಲಿನ ನಾವೀನ್ಯತೆಗಳು ಉದ್ಯಮದ ಅಭಿವೃದ್ಧಿಯನ್ನು ಚಾಲನೆ ಮಾಡಲು ನಿರ್ಣಾಯಕವಾಗಿವೆ. ಪ್ಲಾಸ್ಮಾ ಕತ್ತರಿಸುವ ತಂತ್ರಜ್ಞಾನವು ಅದರ ಹೆಚ್ಚಿನ ನಿಖರತೆ, ದಕ್ಷತೆ ಮತ್ತು ಸಂಕೀರ್ಣ ವೇಫರ್ ಆಕಾರಗಳನ್ನು ನಿರ್ವಹಿಸುವ ಸಾಮರ್ಥ್ಯದೊಂದಿಗೆ, ಈ ಕ್ಷೇತ್ರದಲ್ಲಿ ಗಮನಾರ್ಹ ಹೊಸ ಆಟಗಾರನಾಗಿ ಹೊರಹೊಮ್ಮಿದೆ. ಕೆಲವು ಸವಾಲುಗಳು ಉಳಿದಿದ್ದರೂ, ಈ ಸಮಸ್ಯೆಗಳನ್ನು ಕ್ರಮೇಣವಾಗಿ ಮುಂದುವರಿದ ತಾಂತ್ರಿಕ ನಾವೀನ್ಯತೆಯೊಂದಿಗೆ ಪರಿಹರಿಸಲಾಗುವುದು, ಅರೆವಾಹಕ ಉತ್ಪಾದನೆಗೆ ಹೆಚ್ಚಿನ ಸಾಧ್ಯತೆಗಳು ಮತ್ತು ಅವಕಾಶಗಳನ್ನು ತರುತ್ತದೆ.
ಪ್ಲಾಸ್ಮಾ ಕತ್ತರಿಸುವ ತಂತ್ರಜ್ಞಾನದ ಅನ್ವಯಿಕ ನಿರೀಕ್ಷೆಗಳು ವಿಶಾಲವಾಗಿವೆ ಮತ್ತು ಭವಿಷ್ಯದಲ್ಲಿ ಅರೆವಾಹಕ ತಯಾರಿಕೆಯಲ್ಲಿ ಇದು ಹೆಚ್ಚು ಪ್ರಮುಖ ಪಾತ್ರವನ್ನು ವಹಿಸುವ ನಿರೀಕ್ಷೆಯಿದೆ. ನಿರಂತರ ತಾಂತ್ರಿಕ ನಾವೀನ್ಯತೆ ಮತ್ತು ಆಪ್ಟಿಮೈಸೇಶನ್ ಮೂಲಕ, ಪ್ಲಾಸ್ಮಾ ಕತ್ತರಿಸುವಿಕೆಯು ಅಸ್ತಿತ್ವದಲ್ಲಿರುವ ಸವಾಲುಗಳನ್ನು ಪರಿಹರಿಸುವುದಲ್ಲದೆ, ಅರೆವಾಹಕ ಉದ್ಯಮದ ಬೆಳವಣಿಗೆಯ ಪ್ರಬಲ ಚಾಲಕವಾಗುತ್ತದೆ.
2.4 ಗುಣಮಟ್ಟವನ್ನು ಕಡಿಮೆ ಮಾಡುವುದು ಮತ್ತು ಪ್ರಭಾವ ಬೀರುವ ಅಂಶಗಳು
ನಂತರದ ಚಿಪ್ ಪ್ಯಾಕೇಜಿಂಗ್, ಪರೀಕ್ಷೆ ಮತ್ತು ಅಂತಿಮ ಉತ್ಪನ್ನದ ಒಟ್ಟಾರೆ ಕಾರ್ಯಕ್ಷಮತೆ ಮತ್ತು ವಿಶ್ವಾಸಾರ್ಹತೆಗೆ ವೇಫರ್ ಕತ್ತರಿಸುವ ಗುಣಮಟ್ಟವು ನಿರ್ಣಾಯಕವಾಗಿದೆ. ಕತ್ತರಿಸುವಾಗ ಎದುರಾಗುವ ಸಾಮಾನ್ಯ ಸಮಸ್ಯೆಗಳಲ್ಲಿ ಬಿರುಕುಗಳು, ಚಿಪ್ಪಿಂಗ್ ಮತ್ತು ಕತ್ತರಿಸುವ ವಿಚಲನಗಳು ಸೇರಿವೆ. ಈ ಸಮಸ್ಯೆಗಳು ಹಲವಾರು ಅಂಶಗಳು ಒಟ್ಟಾಗಿ ಕೆಲಸ ಮಾಡುವುದರಿಂದ ಪ್ರಭಾವಿತವಾಗಿರುತ್ತದೆ.
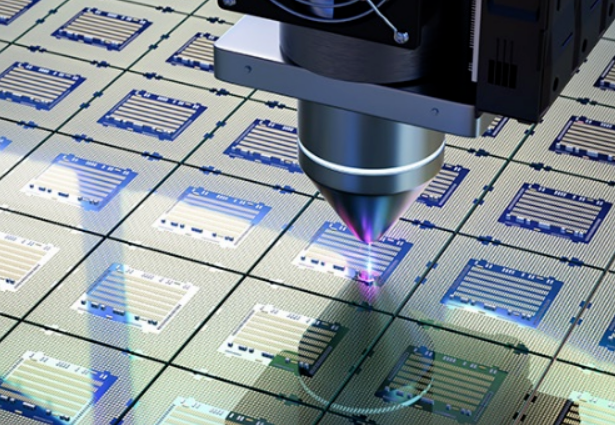
ವರ್ಗ | ವಿಷಯ | ಪರಿಣಾಮ |
ಪ್ರಕ್ರಿಯೆ ನಿಯತಾಂಕಗಳು | ಕತ್ತರಿಸುವ ವೇಗ, ಫೀಡ್ ದರ ಮತ್ತು ಕತ್ತರಿಸುವ ಆಳವು ಕತ್ತರಿಸುವ ಪ್ರಕ್ರಿಯೆಯ ಸ್ಥಿರತೆ ಮತ್ತು ನಿಖರತೆಯ ಮೇಲೆ ನೇರವಾಗಿ ಪರಿಣಾಮ ಬೀರುತ್ತದೆ. ಅನುಚಿತ ಸೆಟ್ಟಿಂಗ್ಗಳು ಒತ್ತಡದ ಸಾಂದ್ರತೆ ಮತ್ತು ಅತಿಯಾದ ಶಾಖ-ಪೀಡಿತ ವಲಯಕ್ಕೆ ಕಾರಣವಾಗಬಹುದು, ಇದರ ಪರಿಣಾಮವಾಗಿ ಬಿರುಕುಗಳು ಮತ್ತು ಚಿಪ್ಪಿಂಗ್ ಉಂಟಾಗುತ್ತದೆ. ವೇಫರ್ ವಸ್ತು, ದಪ್ಪ ಮತ್ತು ಕತ್ತರಿಸುವ ಅವಶ್ಯಕತೆಗಳನ್ನು ಆಧರಿಸಿ ಸೂಕ್ತವಾಗಿ ನಿಯತಾಂಕಗಳನ್ನು ಹೊಂದಿಸುವುದು ಅಪೇಕ್ಷಿತ ಕತ್ತರಿಸುವ ಫಲಿತಾಂಶಗಳನ್ನು ಸಾಧಿಸಲು ಪ್ರಮುಖವಾಗಿದೆ. | ಸರಿಯಾದ ಪ್ರಕ್ರಿಯೆಯ ನಿಯತಾಂಕಗಳು ನಿಖರವಾದ ಕತ್ತರಿಸುವಿಕೆಯನ್ನು ಖಚಿತಪಡಿಸುತ್ತವೆ ಮತ್ತು ಬಿರುಕುಗಳು ಮತ್ತು ಚಿಪ್ಪಿಂಗ್ನಂತಹ ದೋಷಗಳ ಅಪಾಯವನ್ನು ಕಡಿಮೆ ಮಾಡುತ್ತವೆ. |
ಸಲಕರಣೆಗಳು ಮತ್ತು ವಸ್ತು ಅಂಶಗಳು | -ಬ್ಲೇಡ್ ಗುಣಮಟ್ಟ: ಬ್ಲೇಡ್ನ ವಸ್ತು, ಗಡಸುತನ ಮತ್ತು ಉಡುಗೆ ಪ್ರತಿರೋಧವು ಕತ್ತರಿಸುವ ಪ್ರಕ್ರಿಯೆಯ ಮೃದುತ್ವ ಮತ್ತು ಕತ್ತರಿಸಿದ ಮೇಲ್ಮೈಯ ಚಪ್ಪಟೆತನದ ಮೇಲೆ ಪ್ರಭಾವ ಬೀರುತ್ತದೆ. ಕಳಪೆ-ಗುಣಮಟ್ಟದ ಬ್ಲೇಡ್ಗಳು ಘರ್ಷಣೆ ಮತ್ತು ಉಷ್ಣ ಒತ್ತಡವನ್ನು ಹೆಚ್ಚಿಸುತ್ತವೆ, ಇದು ಬಿರುಕುಗಳು ಅಥವಾ ಚಿಪ್ಪಿಂಗ್ಗೆ ಕಾರಣವಾಗಬಹುದು. ಸರಿಯಾದ ಬ್ಲೇಡ್ ವಸ್ತುವನ್ನು ಆಯ್ಕೆ ಮಾಡುವುದು ಬಹಳ ಮುಖ್ಯ. -ಶೀತಕದ ಕಾರ್ಯಕ್ಷಮತೆ: ಕೂಲಂಟ್ಗಳು ಕತ್ತರಿಸುವ ತಾಪಮಾನವನ್ನು ಕಡಿಮೆ ಮಾಡಲು, ಘರ್ಷಣೆಯನ್ನು ಕಡಿಮೆ ಮಾಡಲು ಮತ್ತು ಶಿಲಾಖಂಡರಾಶಿಗಳನ್ನು ತೆರವುಗೊಳಿಸಲು ಸಹಾಯ ಮಾಡುತ್ತದೆ. ನಿಷ್ಪರಿಣಾಮಕಾರಿಯಾದ ಕೂಲಂಟ್ ಹೆಚ್ಚಿನ ತಾಪಮಾನ ಮತ್ತು ಶಿಲಾಖಂಡರಾಶಿಗಳ ಸಂಗ್ರಹಕ್ಕೆ ಕಾರಣವಾಗಬಹುದು, ಇದು ಕತ್ತರಿಸುವ ಗುಣಮಟ್ಟ ಮತ್ತು ದಕ್ಷತೆಯ ಮೇಲೆ ಪರಿಣಾಮ ಬೀರುತ್ತದೆ. ದಕ್ಷ ಮತ್ತು ಪರಿಸರ ಸ್ನೇಹಿ ಕೂಲಂಟ್ಗಳನ್ನು ಆಯ್ಕೆ ಮಾಡುವುದು ಅತ್ಯಗತ್ಯ. | ಬ್ಲೇಡ್ ಗುಣಮಟ್ಟವು ಕಟ್ನ ನಿಖರತೆ ಮತ್ತು ಮೃದುತ್ವದ ಮೇಲೆ ಪರಿಣಾಮ ಬೀರುತ್ತದೆ. ನಿಷ್ಪರಿಣಾಮಕಾರಿಯಾದ ಕೂಲಂಟ್ ಕಳಪೆ ಕತ್ತರಿಸುವ ಗುಣಮಟ್ಟ ಮತ್ತು ದಕ್ಷತೆಗೆ ಕಾರಣವಾಗಬಹುದು, ಇದು ಅತ್ಯುತ್ತಮ ಕೂಲಂಟ್ ಬಳಕೆಯ ಅಗತ್ಯವನ್ನು ಎತ್ತಿ ತೋರಿಸುತ್ತದೆ. |
ಪ್ರಕ್ರಿಯೆ ನಿಯಂತ್ರಣ ಮತ್ತು ಗುಣಮಟ್ಟ ಪರಿಶೀಲನೆ | -ಪ್ರಕ್ರಿಯೆ ನಿಯಂತ್ರಣ: ಕತ್ತರಿಸುವ ಪ್ರಕ್ರಿಯೆಯಲ್ಲಿ ಸ್ಥಿರತೆ ಮತ್ತು ಸ್ಥಿರತೆಯನ್ನು ಖಚಿತಪಡಿಸಿಕೊಳ್ಳಲು ಕೀ ಕತ್ತರಿಸುವ ನಿಯತಾಂಕಗಳ ನೈಜ-ಸಮಯದ ಮೇಲ್ವಿಚಾರಣೆ ಮತ್ತು ಹೊಂದಾಣಿಕೆ. -ಗುಣಮಟ್ಟ ತಪಾಸಣೆ: ಕತ್ತರಿಸುವಿಕೆಯ ನಂತರದ ಗೋಚರತೆ ಪರಿಶೀಲನೆಗಳು, ಆಯಾಮದ ಅಳತೆಗಳು ಮತ್ತು ವಿದ್ಯುತ್ ಕಾರ್ಯಕ್ಷಮತೆ ಪರೀಕ್ಷೆಗಳು ಗುಣಮಟ್ಟದ ಸಮಸ್ಯೆಗಳನ್ನು ತ್ವರಿತವಾಗಿ ಗುರುತಿಸಲು ಮತ್ತು ಪರಿಹರಿಸಲು ಸಹಾಯ ಮಾಡುತ್ತದೆ, ಕತ್ತರಿಸುವ ನಿಖರತೆ ಮತ್ತು ಸ್ಥಿರತೆಯನ್ನು ಸುಧಾರಿಸುತ್ತದೆ. | ಸರಿಯಾದ ಪ್ರಕ್ರಿಯೆ ನಿಯಂತ್ರಣ ಮತ್ತು ಗುಣಮಟ್ಟದ ಪರಿಶೀಲನೆಯು ಸ್ಥಿರವಾದ, ಉತ್ತಮ-ಗುಣಮಟ್ಟದ ಕತ್ತರಿಸುವ ಫಲಿತಾಂಶಗಳನ್ನು ಮತ್ತು ಸಂಭಾವ್ಯ ಸಮಸ್ಯೆಗಳ ಆರಂಭಿಕ ಪತ್ತೆಹಚ್ಚುವಿಕೆಯನ್ನು ಖಚಿತಪಡಿಸಿಕೊಳ್ಳಲು ಸಹಾಯ ಮಾಡುತ್ತದೆ. |

ಕತ್ತರಿಸುವ ಗುಣಮಟ್ಟವನ್ನು ಸುಧಾರಿಸುವುದು
ಕತ್ತರಿಸುವ ಗುಣಮಟ್ಟವನ್ನು ಸುಧಾರಿಸಲು ಪ್ರಕ್ರಿಯೆಯ ನಿಯತಾಂಕಗಳು, ಉಪಕರಣಗಳು ಮತ್ತು ವಸ್ತುಗಳ ಆಯ್ಕೆ, ಪ್ರಕ್ರಿಯೆ ನಿಯಂತ್ರಣ ಮತ್ತು ತಪಾಸಣೆಯನ್ನು ಗಣನೆಗೆ ತೆಗೆದುಕೊಳ್ಳುವ ಸಮಗ್ರ ವಿಧಾನದ ಅಗತ್ಯವಿದೆ. ಕತ್ತರಿಸುವ ತಂತ್ರಜ್ಞಾನಗಳನ್ನು ನಿರಂತರವಾಗಿ ಪರಿಷ್ಕರಿಸುವ ಮೂಲಕ ಮತ್ತು ಪ್ರಕ್ರಿಯೆಯ ವಿಧಾನಗಳನ್ನು ಉತ್ತಮಗೊಳಿಸುವ ಮೂಲಕ, ವೇಫರ್ ಕತ್ತರಿಸುವಿಕೆಯ ನಿಖರತೆ ಮತ್ತು ಸ್ಥಿರತೆಯನ್ನು ಮತ್ತಷ್ಟು ಹೆಚ್ಚಿಸಬಹುದು, ಅರೆವಾಹಕ ಉತ್ಪಾದನಾ ಉದ್ಯಮಕ್ಕೆ ಹೆಚ್ಚು ವಿಶ್ವಾಸಾರ್ಹ ತಾಂತ್ರಿಕ ಬೆಂಬಲವನ್ನು ಒದಗಿಸುತ್ತದೆ.
#03 ಕಟಿಂಗ್ ನಂತರದ ನಿರ್ವಹಣೆ ಮತ್ತು ಪರೀಕ್ಷೆ
3.1 ಸ್ವಚ್ಛಗೊಳಿಸುವಿಕೆ ಮತ್ತು ಒಣಗಿಸುವಿಕೆ
ಚಿಪ್ ಗುಣಮಟ್ಟ ಮತ್ತು ನಂತರದ ಪ್ರಕ್ರಿಯೆಗಳ ಸುಗಮ ಪ್ರಗತಿಯನ್ನು ಖಚಿತಪಡಿಸಿಕೊಳ್ಳಲು ವೇಫರ್ ಕತ್ತರಿಸಿದ ನಂತರ ಸ್ವಚ್ಛಗೊಳಿಸುವ ಮತ್ತು ಒಣಗಿಸುವ ಹಂತಗಳು ನಿರ್ಣಾಯಕವಾಗಿವೆ. ಈ ಹಂತದಲ್ಲಿ, ಕತ್ತರಿಸುವಾಗ ಉತ್ಪತ್ತಿಯಾಗುವ ಸಿಲಿಕಾನ್ ಶಿಲಾಖಂಡರಾಶಿಗಳು, ಶೀತಕ ಶೇಷ ಮತ್ತು ಇತರ ಮಾಲಿನ್ಯಕಾರಕಗಳನ್ನು ಸಂಪೂರ್ಣವಾಗಿ ತೆಗೆದುಹಾಕುವುದು ಅತ್ಯಗತ್ಯ. ಶುಚಿಗೊಳಿಸುವ ಪ್ರಕ್ರಿಯೆಯಲ್ಲಿ ಚಿಪ್ಸ್ ಹಾನಿಗೊಳಗಾಗದಂತೆ ನೋಡಿಕೊಳ್ಳುವುದು ಮತ್ತು ಒಣಗಿದ ನಂತರ, ತುಕ್ಕು ಅಥವಾ ಸ್ಥಾಯೀವಿದ್ಯುತ್ತಿನ ವಿಸರ್ಜನೆಯಂತಹ ಸಮಸ್ಯೆಗಳನ್ನು ತಡೆಗಟ್ಟಲು ಚಿಪ್ ಮೇಲ್ಮೈಯಲ್ಲಿ ಯಾವುದೇ ತೇವಾಂಶ ಉಳಿಯದಂತೆ ನೋಡಿಕೊಳ್ಳುವುದು ಅಷ್ಟೇ ಮುಖ್ಯ.
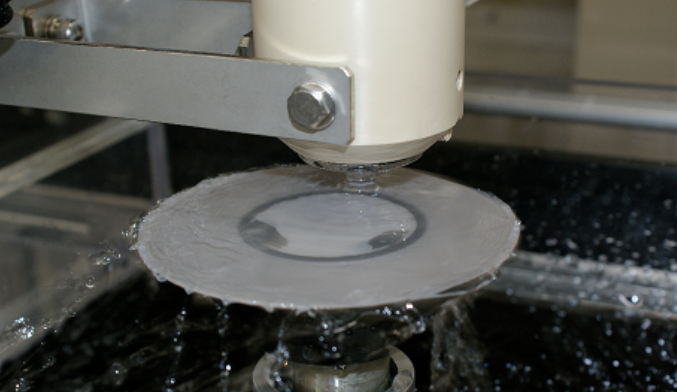
ಕತ್ತರಿಸಿದ ನಂತರದ ನಿರ್ವಹಣೆ: ಸ್ವಚ್ಛಗೊಳಿಸುವ ಮತ್ತು ಒಣಗಿಸುವ ಪ್ರಕ್ರಿಯೆ
ಪ್ರಕ್ರಿಯೆ ಹಂತ | ವಿಷಯ | ಪರಿಣಾಮ |
ಶುಚಿಗೊಳಿಸುವ ಪ್ರಕ್ರಿಯೆ | -ವಿಧಾನ: ಸ್ವಚ್ಛಗೊಳಿಸಲು ಅಲ್ಟ್ರಾಸಾನಿಕ್ ಅಥವಾ ಮೆಕ್ಯಾನಿಕಲ್ ಬ್ರಶಿಂಗ್ ತಂತ್ರಗಳೊಂದಿಗೆ ವಿಶೇಷ ಶುಚಿಗೊಳಿಸುವ ಏಜೆಂಟ್ಗಳು ಮತ್ತು ಶುದ್ಧ ನೀರನ್ನು ಬಳಸಿ. | ಮಾಲಿನ್ಯಕಾರಕಗಳನ್ನು ಸಂಪೂರ್ಣವಾಗಿ ತೆಗೆದುಹಾಕುವುದನ್ನು ಖಚಿತಪಡಿಸುತ್ತದೆ ಮತ್ತು ಸ್ವಚ್ಛಗೊಳಿಸುವ ಸಮಯದಲ್ಲಿ ಚಿಪ್ಗಳಿಗೆ ಹಾನಿಯಾಗದಂತೆ ತಡೆಯುತ್ತದೆ. |
-ಶುಚಿಗೊಳಿಸುವ ಏಜೆಂಟ್ ಆಯ್ಕೆ: ಚಿಪ್ಗೆ ಹಾನಿಯಾಗದಂತೆ ಪರಿಣಾಮಕಾರಿ ಶುಚಿಗೊಳಿಸುವಿಕೆಯನ್ನು ಖಚಿತಪಡಿಸಿಕೊಳ್ಳಲು ವೇಫರ್ ವಸ್ತು ಮತ್ತು ಮಾಲಿನ್ಯಕಾರಕ ಪ್ರಕಾರವನ್ನು ಆಧರಿಸಿ ಆಯ್ಕೆಮಾಡಿ. | ಪರಿಣಾಮಕಾರಿ ಶುಚಿಗೊಳಿಸುವಿಕೆ ಮತ್ತು ಚಿಪ್ ರಕ್ಷಣೆಗೆ ಸರಿಯಾದ ಏಜೆಂಟ್ ಆಯ್ಕೆಯು ಪ್ರಮುಖವಾಗಿದೆ. | |
-ನಿಯತಾಂಕ ನಿಯಂತ್ರಣ: ಅನುಚಿತ ಶುಚಿಗೊಳಿಸುವಿಕೆಯಿಂದ ಉಂಟಾಗುವ ಗುಣಮಟ್ಟದ ಸಮಸ್ಯೆಗಳನ್ನು ತಡೆಗಟ್ಟಲು ಶುಚಿಗೊಳಿಸುವ ತಾಪಮಾನ, ಸಮಯ ಮತ್ತು ಶುಚಿಗೊಳಿಸುವ ದ್ರಾವಣದ ಸಾಂದ್ರತೆಯನ್ನು ಕಟ್ಟುನಿಟ್ಟಾಗಿ ನಿಯಂತ್ರಿಸಿ. | ನಿಯಂತ್ರಣಗಳು ವೇಫರ್ಗೆ ಹಾನಿಯಾಗುವುದನ್ನು ಅಥವಾ ಮಾಲಿನ್ಯಕಾರಕಗಳನ್ನು ಬಿಡುವುದನ್ನು ತಪ್ಪಿಸಲು ಸಹಾಯ ಮಾಡುತ್ತದೆ, ಇದು ಸ್ಥಿರವಾದ ಗುಣಮಟ್ಟವನ್ನು ಖಚಿತಪಡಿಸುತ್ತದೆ. | |
ಒಣಗಿಸುವ ಪ್ರಕ್ರಿಯೆ | -ಸಾಂಪ್ರದಾಯಿಕ ವಿಧಾನಗಳು: ನೈಸರ್ಗಿಕ ಗಾಳಿಯಲ್ಲಿ ಒಣಗಿಸುವುದು ಮತ್ತು ಬಿಸಿ ಗಾಳಿಯಲ್ಲಿ ಒಣಗಿಸುವುದು, ಇವು ಕಡಿಮೆ ದಕ್ಷತೆಯನ್ನು ಹೊಂದಿರುತ್ತವೆ ಮತ್ತು ಸ್ಥಿರ ವಿದ್ಯುತ್ ಸಂಗ್ರಹಕ್ಕೆ ಕಾರಣವಾಗಬಹುದು. | ನಿಧಾನವಾದ ಒಣಗಿಸುವ ಸಮಯ ಮತ್ತು ಸಂಭಾವ್ಯ ಸ್ಥಿರ ಸಮಸ್ಯೆಗಳಿಗೆ ಕಾರಣವಾಗಬಹುದು. |
-ಆಧುನಿಕ ತಂತ್ರಜ್ಞಾನಗಳು: ಚಿಪ್ಸ್ ಬೇಗನೆ ಒಣಗುವುದನ್ನು ಮತ್ತು ಹಾನಿಕಾರಕ ಪರಿಣಾಮಗಳನ್ನು ತಪ್ಪಿಸುವುದನ್ನು ಖಚಿತಪಡಿಸಿಕೊಳ್ಳಲು ನಿರ್ವಾತ ಒಣಗಿಸುವಿಕೆ ಮತ್ತು ಅತಿಗೆಂಪು ಒಣಗಿಸುವಿಕೆಯಂತಹ ಸುಧಾರಿತ ತಂತ್ರಜ್ಞಾನಗಳನ್ನು ಬಳಸಿ. | ವೇಗವಾದ ಮತ್ತು ಹೆಚ್ಚು ಪರಿಣಾಮಕಾರಿಯಾದ ಒಣಗಿಸುವ ಪ್ರಕ್ರಿಯೆ, ಸ್ಥಿರ ವಿಸರ್ಜನೆ ಅಥವಾ ತೇವಾಂಶ-ಸಂಬಂಧಿತ ಸಮಸ್ಯೆಗಳ ಅಪಾಯವನ್ನು ಕಡಿಮೆ ಮಾಡುತ್ತದೆ. | |
ಸಲಕರಣೆಗಳ ಆಯ್ಕೆ ಮತ್ತು ನಿರ್ವಹಣೆ | -ಸಲಕರಣೆಗಳ ಆಯ್ಕೆ: ಹೆಚ್ಚಿನ ಕಾರ್ಯಕ್ಷಮತೆಯ ಶುಚಿಗೊಳಿಸುವ ಮತ್ತು ಒಣಗಿಸುವ ಯಂತ್ರಗಳು ಸಂಸ್ಕರಣಾ ದಕ್ಷತೆಯನ್ನು ಸುಧಾರಿಸುತ್ತದೆ ಮತ್ತು ನಿರ್ವಹಣೆಯ ಸಮಯದಲ್ಲಿ ಸಂಭಾವ್ಯ ಸಮಸ್ಯೆಗಳನ್ನು ಸೂಕ್ಷ್ಮವಾಗಿ ನಿಯಂತ್ರಿಸುತ್ತವೆ. | ಉತ್ತಮ ಗುಣಮಟ್ಟದ ಯಂತ್ರಗಳು ಉತ್ತಮ ಸಂಸ್ಕರಣೆಯನ್ನು ಖಚಿತಪಡಿಸುತ್ತವೆ ಮತ್ತು ಸ್ವಚ್ಛಗೊಳಿಸುವ ಮತ್ತು ಒಣಗಿಸುವ ಸಮಯದಲ್ಲಿ ದೋಷಗಳ ಸಾಧ್ಯತೆಯನ್ನು ಕಡಿಮೆ ಮಾಡುತ್ತವೆ. |
-ಸಲಕರಣೆ ನಿರ್ವಹಣೆ: ಉಪಕರಣಗಳ ನಿಯಮಿತ ತಪಾಸಣೆ ಮತ್ತು ನಿರ್ವಹಣೆಯು ಅದು ಅತ್ಯುತ್ತಮ ಕೆಲಸದ ಸ್ಥಿತಿಯಲ್ಲಿರುವುದನ್ನು ಖಚಿತಪಡಿಸುತ್ತದೆ, ಚಿಪ್ ಗುಣಮಟ್ಟವನ್ನು ಖಾತರಿಪಡಿಸುತ್ತದೆ. | ಸರಿಯಾದ ನಿರ್ವಹಣೆಯು ಸಲಕರಣೆಗಳ ವೈಫಲ್ಯಗಳನ್ನು ತಡೆಯುತ್ತದೆ, ವಿಶ್ವಾಸಾರ್ಹ ಮತ್ತು ಉತ್ತಮ-ಗುಣಮಟ್ಟದ ಸಂಸ್ಕರಣೆಯನ್ನು ಖಚಿತಪಡಿಸುತ್ತದೆ. |
ಕತ್ತರಿಸಿದ ನಂತರ ಸ್ವಚ್ಛಗೊಳಿಸುವುದು ಮತ್ತು ಒಣಗಿಸುವುದು
ವೇಫರ್ ಕತ್ತರಿಸಿದ ನಂತರ ಸ್ವಚ್ಛಗೊಳಿಸುವ ಮತ್ತು ಒಣಗಿಸುವ ಹಂತಗಳು ಸಂಕೀರ್ಣ ಮತ್ತು ಸೂಕ್ಷ್ಮ ಪ್ರಕ್ರಿಯೆಗಳಾಗಿದ್ದು, ಅಂತಿಮ ಸಂಸ್ಕರಣಾ ಫಲಿತಾಂಶವನ್ನು ಖಚಿತಪಡಿಸಿಕೊಳ್ಳಲು ಬಹು ಅಂಶಗಳನ್ನು ಎಚ್ಚರಿಕೆಯಿಂದ ಪರಿಗಣಿಸುವ ಅಗತ್ಯವಿರುತ್ತದೆ. ವೈಜ್ಞಾನಿಕ ವಿಧಾನಗಳು ಮತ್ತು ಕಠಿಣ ಕಾರ್ಯವಿಧಾನಗಳನ್ನು ಬಳಸುವುದರ ಮೂಲಕ, ಪ್ರತಿ ಚಿಪ್ ನಂತರದ ಪ್ಯಾಕೇಜಿಂಗ್ ಮತ್ತು ಪರೀಕ್ಷಾ ಹಂತಗಳನ್ನು ಸೂಕ್ತ ಸ್ಥಿತಿಯಲ್ಲಿ ಪ್ರವೇಶಿಸುತ್ತದೆ ಎಂದು ಖಚಿತಪಡಿಸಿಕೊಳ್ಳಲು ಸಾಧ್ಯವಿದೆ.
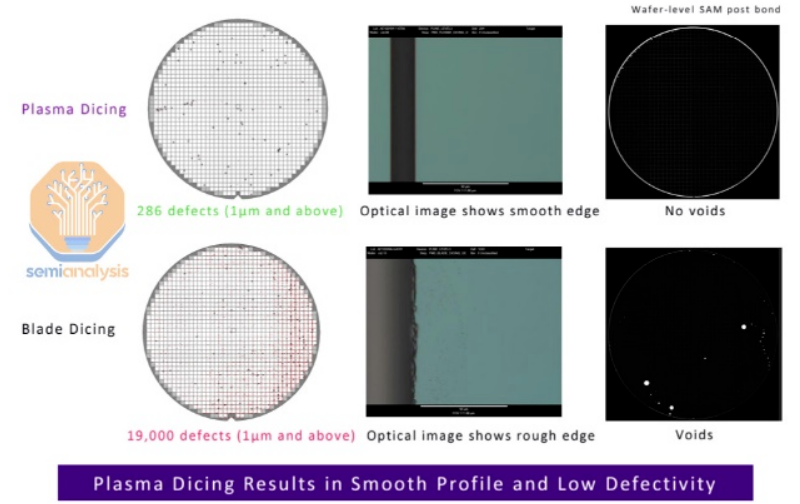
ಕತ್ತರಿಸಿದ ನಂತರದ ಪರಿಶೀಲನೆ ಮತ್ತು ಪರೀಕ್ಷೆ
ನಡೆಯಿರಿ | ವಿಷಯ | ಪರಿಣಾಮ |
ತಪಾಸಣೆ ಹಂತ | 1.ದೃಶ್ಯ ತಪಾಸಣೆ: ಚಿಪ್ ಮೇಲ್ಮೈಯಲ್ಲಿ ಬಿರುಕುಗಳು, ಚಿಪ್ಪಿಂಗ್ ಅಥವಾ ಮಾಲಿನ್ಯದಂತಹ ಗೋಚರ ದೋಷಗಳನ್ನು ಪರಿಶೀಲಿಸಲು ದೃಶ್ಯ ಅಥವಾ ಸ್ವಯಂಚಾಲಿತ ತಪಾಸಣಾ ಸಾಧನಗಳನ್ನು ಬಳಸಿ. ತ್ಯಾಜ್ಯವನ್ನು ತಪ್ಪಿಸಲು ಭೌತಿಕವಾಗಿ ಹಾನಿಗೊಳಗಾದ ಚಿಪ್ಗಳನ್ನು ತ್ವರಿತವಾಗಿ ಗುರುತಿಸಿ. | ಪ್ರಕ್ರಿಯೆಯ ಆರಂಭಿಕ ಹಂತಗಳಲ್ಲಿ ದೋಷಯುಕ್ತ ಚಿಪ್ಗಳನ್ನು ಗುರುತಿಸಲು ಮತ್ತು ತೆಗೆದುಹಾಕಲು ಸಹಾಯ ಮಾಡುತ್ತದೆ, ಇದರಿಂದಾಗಿ ವಸ್ತು ನಷ್ಟವನ್ನು ಕಡಿಮೆ ಮಾಡುತ್ತದೆ. |
2.ಗಾತ್ರ ಮಾಪನ: ಚಿಪ್ ಆಯಾಮಗಳನ್ನು ನಿಖರವಾಗಿ ಅಳೆಯಲು ನಿಖರ ಅಳತೆ ಸಾಧನಗಳನ್ನು ಬಳಸಿ, ಕತ್ತರಿಸಿದ ಗಾತ್ರವು ವಿನ್ಯಾಸ ವಿಶೇಷಣಗಳನ್ನು ಪೂರೈಸುತ್ತದೆ ಮತ್ತು ಕಾರ್ಯಕ್ಷಮತೆಯ ಸಮಸ್ಯೆಗಳು ಅಥವಾ ಪ್ಯಾಕೇಜಿಂಗ್ ತೊಂದರೆಗಳನ್ನು ತಡೆಯುತ್ತದೆ ಎಂದು ಖಚಿತಪಡಿಸಿಕೊಳ್ಳಿ. | ಚಿಪ್ಗಳು ಅಗತ್ಯವಿರುವ ಗಾತ್ರದ ಮಿತಿಯೊಳಗೆ ಇರುವುದನ್ನು ಖಚಿತಪಡಿಸುತ್ತದೆ, ಕಾರ್ಯಕ್ಷಮತೆಯ ಅವನತಿ ಅಥವಾ ಜೋಡಣೆ ಸಮಸ್ಯೆಗಳನ್ನು ತಡೆಯುತ್ತದೆ. | |
3.ವಿದ್ಯುತ್ ಕಾರ್ಯಕ್ಷಮತೆ ಪರೀಕ್ಷೆ: ಅನುಸರಣೆಯಿಲ್ಲದ ಚಿಪ್ಗಳನ್ನು ಗುರುತಿಸಲು ಮತ್ತು ಕಾರ್ಯಕ್ಷಮತೆ-ಅರ್ಹ ಚಿಪ್ಗಳು ಮಾತ್ರ ಮುಂದಿನ ಹಂತಕ್ಕೆ ಮುಂದುವರಿಯುವುದನ್ನು ಖಚಿತಪಡಿಸಿಕೊಳ್ಳಲು ಪ್ರತಿರೋಧ, ಕೆಪಾಸಿಟನ್ಸ್ ಮತ್ತು ಇಂಡಕ್ಟನ್ಸ್ನಂತಹ ಪ್ರಮುಖ ವಿದ್ಯುತ್ ನಿಯತಾಂಕಗಳನ್ನು ಮೌಲ್ಯಮಾಪನ ಮಾಡಿ. | ಪ್ರಕ್ರಿಯೆಯಲ್ಲಿ ಕ್ರಿಯಾತ್ಮಕ ಮತ್ತು ಕಾರ್ಯಕ್ಷಮತೆ-ಪರೀಕ್ಷಿತ ಚಿಪ್ಗಳು ಮಾತ್ರ ಮುಂದುವರಿಯುವುದನ್ನು ಖಚಿತಪಡಿಸುತ್ತದೆ, ನಂತರದ ಹಂತಗಳಲ್ಲಿ ವೈಫಲ್ಯದ ಅಪಾಯವನ್ನು ಕಡಿಮೆ ಮಾಡುತ್ತದೆ. | |
ಪರೀಕ್ಷಾ ಹಂತ | 1.ಕ್ರಿಯಾತ್ಮಕ ಪರೀಕ್ಷೆ: ಚಿಪ್ನ ಮೂಲ ಕಾರ್ಯಚಟುವಟಿಕೆಯು ಉದ್ದೇಶಿಸಿದಂತೆ ಕಾರ್ಯನಿರ್ವಹಿಸುತ್ತದೆಯೇ ಎಂದು ಪರಿಶೀಲಿಸಿ, ಕ್ರಿಯಾತ್ಮಕ ಅಸಹಜತೆಗಳೊಂದಿಗೆ ಚಿಪ್ಗಳನ್ನು ಗುರುತಿಸುತ್ತದೆ ಮತ್ತು ತೆಗೆದುಹಾಕುತ್ತದೆ. | ನಂತರದ ಹಂತಗಳಿಗೆ ಮುಂದುವರಿಯುವ ಮೊದಲು ಚಿಪ್ಗಳು ಮೂಲಭೂತ ಕಾರ್ಯಾಚರಣೆಯ ಅವಶ್ಯಕತೆಗಳನ್ನು ಪೂರೈಸುತ್ತವೆ ಎಂದು ಖಚಿತಪಡಿಸುತ್ತದೆ. |
2.ವಿಶ್ವಾಸಾರ್ಹತೆ ಪರೀಕ್ಷೆ: ದೀರ್ಘಾವಧಿಯ ಬಳಕೆ ಅಥವಾ ಕಠಿಣ ಪರಿಸರದಲ್ಲಿ ಚಿಪ್ ಕಾರ್ಯಕ್ಷಮತೆಯ ಸ್ಥಿರತೆಯನ್ನು ಮೌಲ್ಯಮಾಪನ ಮಾಡಿ, ಸಾಮಾನ್ಯವಾಗಿ ಹೆಚ್ಚಿನ-ತಾಪಮಾನದ ವಯಸ್ಸಾದಿಕೆ, ಕಡಿಮೆ-ತಾಪಮಾನದ ಪರೀಕ್ಷೆ ಮತ್ತು ನೈಜ-ಪ್ರಪಂಚದ ವಿಪರೀತ ಪರಿಸ್ಥಿತಿಗಳನ್ನು ಅನುಕರಿಸಲು ಆರ್ದ್ರತೆಯ ಪರೀಕ್ಷೆಯನ್ನು ಒಳಗೊಂಡಿರುತ್ತದೆ. | ಚಿಪ್ಸ್ ವಿವಿಧ ಪರಿಸರ ಪರಿಸ್ಥಿತಿಗಳಲ್ಲಿ ವಿಶ್ವಾಸಾರ್ಹವಾಗಿ ಕಾರ್ಯನಿರ್ವಹಿಸುತ್ತದೆ ಎಂದು ಖಚಿತಪಡಿಸುತ್ತದೆ, ಉತ್ಪನ್ನದ ದೀರ್ಘಾಯುಷ್ಯ ಮತ್ತು ಸ್ಥಿರತೆಯನ್ನು ಸುಧಾರಿಸುತ್ತದೆ. | |
3.ಹೊಂದಾಣಿಕೆ ಪರೀಕ್ಷೆ: ಚಿಪ್ ಇತರ ಘಟಕಗಳು ಅಥವಾ ವ್ಯವಸ್ಥೆಗಳೊಂದಿಗೆ ಸರಿಯಾಗಿ ಕಾರ್ಯನಿರ್ವಹಿಸುತ್ತದೆಯೇ ಎಂದು ಪರಿಶೀಲಿಸಿ, ಹೊಂದಾಣಿಕೆಯಾಗದ ಕಾರಣ ಯಾವುದೇ ದೋಷಗಳು ಅಥವಾ ಕಾರ್ಯಕ್ಷಮತೆಯ ಅವನತಿ ಇಲ್ಲ ಎಂದು ಖಚಿತಪಡಿಸಿಕೊಳ್ಳಿ. | ಹೊಂದಾಣಿಕೆಯ ಸಮಸ್ಯೆಗಳನ್ನು ತಡೆಗಟ್ಟುವ ಮೂಲಕ ನೈಜ-ಪ್ರಪಂಚದ ಅಪ್ಲಿಕೇಶನ್ಗಳಲ್ಲಿ ಸುಗಮ ಕಾರ್ಯಾಚರಣೆಯನ್ನು ಖಚಿತಪಡಿಸುತ್ತದೆ. |
3.3 ಪ್ಯಾಕೇಜಿಂಗ್ ಮತ್ತು ಸಂಗ್ರಹಣೆ
ವೇಫರ್ ಕತ್ತರಿಸುವಿಕೆಯ ನಂತರ, ಚಿಪ್ಗಳು ಅರೆವಾಹಕ ಉತ್ಪಾದನಾ ಪ್ರಕ್ರಿಯೆಯ ನಿರ್ಣಾಯಕ ಉತ್ಪನ್ನವಾಗಿದೆ ಮತ್ತು ಅವುಗಳ ಪ್ಯಾಕೇಜಿಂಗ್ ಮತ್ತು ಶೇಖರಣಾ ಹಂತಗಳು ಸಮಾನವಾಗಿ ಮುಖ್ಯವಾಗಿವೆ. ಸರಿಯಾದ ಪ್ಯಾಕೇಜಿಂಗ್ ಮತ್ತು ಶೇಖರಣಾ ಕ್ರಮಗಳು ಸಾಗಣೆ ಮತ್ತು ಶೇಖರಣಾ ಸಮಯದಲ್ಲಿ ಚಿಪ್ಗಳ ಸುರಕ್ಷತೆ ಮತ್ತು ಸ್ಥಿರತೆಯನ್ನು ಖಚಿತಪಡಿಸಿಕೊಳ್ಳಲು ಮಾತ್ರವಲ್ಲದೆ ನಂತರದ ಉತ್ಪಾದನೆ, ಪರೀಕ್ಷೆ ಮತ್ತು ಪ್ಯಾಕೇಜಿಂಗ್ ಹಂತಗಳಿಗೆ ಬಲವಾದ ಬೆಂಬಲವನ್ನು ಒದಗಿಸಲು ಸಹ ಅತ್ಯಗತ್ಯ.
ತಪಾಸಣೆ ಮತ್ತು ಪರೀಕ್ಷಾ ಹಂತಗಳ ಸಾರಾಂಶ:
ವೇಫರ್ ಕತ್ತರಿಸಿದ ನಂತರ ಚಿಪ್ಗಳ ತಪಾಸಣೆ ಮತ್ತು ಪರೀಕ್ಷಾ ಹಂತಗಳು ದೃಶ್ಯ ತಪಾಸಣೆ, ಗಾತ್ರ ಮಾಪನ, ವಿದ್ಯುತ್ ಕಾರ್ಯಕ್ಷಮತೆ ಪರೀಕ್ಷೆ, ಕ್ರಿಯಾತ್ಮಕ ಪರೀಕ್ಷೆ, ವಿಶ್ವಾಸಾರ್ಹತೆ ಪರೀಕ್ಷೆ ಮತ್ತು ಹೊಂದಾಣಿಕೆ ಪರೀಕ್ಷೆ ಸೇರಿದಂತೆ ಹಲವಾರು ಅಂಶಗಳನ್ನು ಒಳಗೊಂಡಿವೆ. ಈ ಹಂತಗಳು ಪರಸ್ಪರ ಸಂಬಂಧ ಹೊಂದಿವೆ ಮತ್ತು ಪೂರಕವಾಗಿದ್ದು, ಉತ್ಪನ್ನದ ಗುಣಮಟ್ಟ ಮತ್ತು ವಿಶ್ವಾಸಾರ್ಹತೆಯನ್ನು ಖಚಿತಪಡಿಸಿಕೊಳ್ಳಲು ಘನ ತಡೆಗೋಡೆಯನ್ನು ರೂಪಿಸುತ್ತವೆ. ಕಟ್ಟುನಿಟ್ಟಾದ ತಪಾಸಣೆ ಮತ್ತು ಪರೀಕ್ಷಾ ಕಾರ್ಯವಿಧಾನಗಳ ಮೂಲಕ, ಸಂಭಾವ್ಯ ಸಮಸ್ಯೆಗಳನ್ನು ಗುರುತಿಸಬಹುದು ಮತ್ತು ತ್ವರಿತವಾಗಿ ಪರಿಹರಿಸಬಹುದು, ಅಂತಿಮ ಉತ್ಪನ್ನವು ಗ್ರಾಹಕರ ಅವಶ್ಯಕತೆಗಳು ಮತ್ತು ನಿರೀಕ್ಷೆಗಳನ್ನು ಪೂರೈಸುತ್ತದೆ ಎಂದು ಖಚಿತಪಡಿಸುತ್ತದೆ.
ಅಂಶ | ವಿಷಯ |
ಪ್ಯಾಕೇಜಿಂಗ್ ಅಳತೆಗಳು | 1.ಆಂಟಿ-ಸ್ಟ್ಯಾಟಿಕ್: ಪ್ಯಾಕೇಜಿಂಗ್ ಸಾಮಗ್ರಿಗಳು ಅತ್ಯುತ್ತಮವಾದ ಆಂಟಿ-ಸ್ಟ್ಯಾಟಿಕ್ ಗುಣಲಕ್ಷಣಗಳನ್ನು ಹೊಂದಿರಬೇಕು, ಇದರಿಂದಾಗಿ ಸ್ಥಿರ ವಿದ್ಯುತ್ ಸಾಧನಗಳಿಗೆ ಹಾನಿಯಾಗದಂತೆ ಅಥವಾ ಅವುಗಳ ಕಾರ್ಯಕ್ಷಮತೆಯ ಮೇಲೆ ಪರಿಣಾಮ ಬೀರುವುದನ್ನು ತಡೆಯಬಹುದು. |
2.ತೇವಾಂಶ ನಿರೋಧಕ: ತೇವಾಂಶದಿಂದ ಉಂಟಾಗುವ ವಿದ್ಯುತ್ ಕಾರ್ಯಕ್ಷಮತೆಯ ತುಕ್ಕು ಮತ್ತು ಕ್ಷೀಣತೆಯನ್ನು ತಡೆಗಟ್ಟಲು ಪ್ಯಾಕೇಜಿಂಗ್ ವಸ್ತುಗಳು ಉತ್ತಮ ತೇವಾಂಶ ನಿರೋಧಕತೆಯನ್ನು ಹೊಂದಿರಬೇಕು. | |
3.ಆಘಾತ ನಿರೋಧಕ: ಸಾಗಣೆಯ ಸಮಯದಲ್ಲಿ ಕಂಪನ ಮತ್ತು ಪ್ರಭಾವದಿಂದ ಚಿಪ್ಗಳನ್ನು ರಕ್ಷಿಸಲು ಪ್ಯಾಕೇಜಿಂಗ್ ವಸ್ತುಗಳು ಪರಿಣಾಮಕಾರಿ ಆಘಾತ ಹೀರಿಕೊಳ್ಳುವಿಕೆಯನ್ನು ಒದಗಿಸಬೇಕು. | |
ಶೇಖರಣಾ ಪರಿಸರ | 1.ಆರ್ದ್ರತೆ ನಿಯಂತ್ರಣ: ಅತಿಯಾದ ಆರ್ದ್ರತೆಯಿಂದ ಉಂಟಾಗುವ ತೇವಾಂಶ ಹೀರಿಕೊಳ್ಳುವಿಕೆ ಮತ್ತು ತುಕ್ಕು ಹಿಡಿಯುವುದನ್ನು ಅಥವಾ ಕಡಿಮೆ ಆರ್ದ್ರತೆಯಿಂದ ಉಂಟಾಗುವ ಸ್ಥಿರ ಸಮಸ್ಯೆಗಳನ್ನು ತಡೆಗಟ್ಟಲು ಸೂಕ್ತ ವ್ಯಾಪ್ತಿಯಲ್ಲಿ ಆರ್ದ್ರತೆಯನ್ನು ಕಟ್ಟುನಿಟ್ಟಾಗಿ ನಿಯಂತ್ರಿಸಿ. |
2.ಸ್ವಚ್ಛತೆ: ಧೂಳು ಮತ್ತು ಕಲ್ಮಶಗಳಿಂದ ಚಿಪ್ಸ್ ಕಲುಷಿತವಾಗುವುದನ್ನು ತಪ್ಪಿಸಲು ಸ್ವಚ್ಛವಾದ ಶೇಖರಣಾ ವಾತಾವರಣವನ್ನು ಕಾಪಾಡಿಕೊಳ್ಳಿ. | |
3.ತಾಪಮಾನ ನಿಯಂತ್ರಣ: ಕಡಿಮೆ ತಾಪಮಾನದಿಂದ ಉಂಟಾಗುವ ಅತಿಯಾದ ಶಾಖ ಅಥವಾ ಘನೀಕರಣ ಸಮಸ್ಯೆಗಳಿಂದಾಗಿ ವೇಗವರ್ಧಿತ ವಯಸ್ಸಾಗುವಿಕೆಯನ್ನು ತಡೆಯಲು ಸಮಂಜಸವಾದ ತಾಪಮಾನ ಶ್ರೇಣಿಯನ್ನು ಹೊಂದಿಸಿ ಮತ್ತು ತಾಪಮಾನದ ಸ್ಥಿರತೆಯನ್ನು ಕಾಪಾಡಿಕೊಳ್ಳಿ. | |
ನಿಯಮಿತ ತಪಾಸಣೆ | ದೃಶ್ಯ ತಪಾಸಣೆಗಳು, ಗಾತ್ರ ಮಾಪನಗಳು ಮತ್ತು ವಿದ್ಯುತ್ ಕಾರ್ಯಕ್ಷಮತೆ ಪರೀಕ್ಷೆಗಳನ್ನು ಬಳಸಿಕೊಂಡು ಸಂಗ್ರಹಿಸಲಾದ ಚಿಪ್ಗಳನ್ನು ನಿಯಮಿತವಾಗಿ ಪರಿಶೀಲಿಸಿ ಮತ್ತು ಮೌಲ್ಯಮಾಪನ ಮಾಡಿ, ಸಂಭಾವ್ಯ ಸಮಸ್ಯೆಗಳನ್ನು ಸಮಯೋಚಿತವಾಗಿ ಗುರುತಿಸಿ ಮತ್ತು ಪರಿಹರಿಸಿ. ಶೇಖರಣಾ ಸಮಯ ಮತ್ತು ಪರಿಸ್ಥಿತಿಗಳ ಆಧಾರದ ಮೇಲೆ, ಚಿಪ್ಗಳನ್ನು ಸೂಕ್ತ ಸ್ಥಿತಿಯಲ್ಲಿ ಬಳಸಲಾಗಿದೆಯೆ ಎಂದು ಖಚಿತಪಡಿಸಿಕೊಳ್ಳಲು ಅವುಗಳ ಬಳಕೆಯನ್ನು ಯೋಜಿಸಿ. |
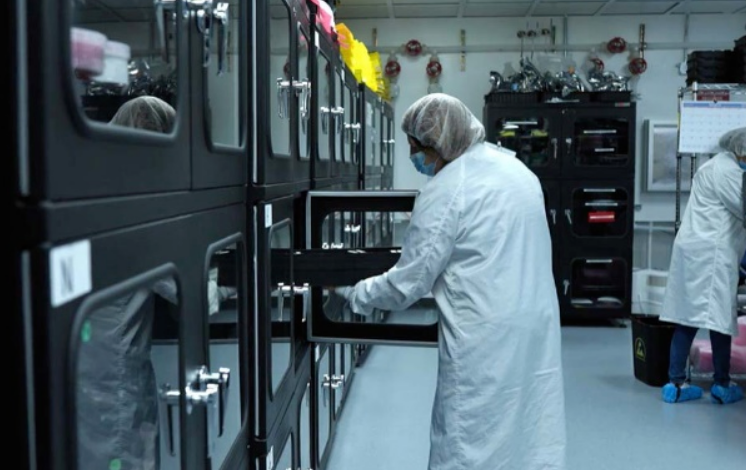
ವೇಫರ್ ಡೈಸಿಂಗ್ ಪ್ರಕ್ರಿಯೆಯ ಸಮಯದಲ್ಲಿ ಮೈಕ್ರೋಕ್ರ್ಯಾಕ್ಗಳು ಮತ್ತು ಹಾನಿಯ ಸಮಸ್ಯೆಯು ಅರೆವಾಹಕ ಉತ್ಪಾದನೆಯಲ್ಲಿ ಗಮನಾರ್ಹ ಸವಾಲಾಗಿದೆ. ಕತ್ತರಿಸುವ ಒತ್ತಡವು ಈ ವಿದ್ಯಮಾನಕ್ಕೆ ಪ್ರಾಥಮಿಕ ಕಾರಣವಾಗಿದೆ, ಏಕೆಂದರೆ ಇದು ವೇಫರ್ ಮೇಲ್ಮೈಯಲ್ಲಿ ಸಣ್ಣ ಬಿರುಕುಗಳು ಮತ್ತು ಹಾನಿಯನ್ನು ಉಂಟುಮಾಡುತ್ತದೆ, ಇದು ಉತ್ಪಾದನಾ ವೆಚ್ಚವನ್ನು ಹೆಚ್ಚಿಸುತ್ತದೆ ಮತ್ತು ಉತ್ಪನ್ನದ ಗುಣಮಟ್ಟದಲ್ಲಿ ಇಳಿಕೆಗೆ ಕಾರಣವಾಗುತ್ತದೆ.
ಈ ಸವಾಲನ್ನು ಎದುರಿಸಲು, ಕತ್ತರಿಸುವ ಒತ್ತಡವನ್ನು ಕಡಿಮೆ ಮಾಡುವುದು ಮತ್ತು ಅತ್ಯುತ್ತಮವಾದ ಕತ್ತರಿಸುವ ತಂತ್ರಗಳು, ಉಪಕರಣಗಳು ಮತ್ತು ಪರಿಸ್ಥಿತಿಗಳನ್ನು ಕಾರ್ಯಗತಗೊಳಿಸುವುದು ಬಹಳ ಮುಖ್ಯ. ಬ್ಲೇಡ್ ವಸ್ತು, ಕತ್ತರಿಸುವ ವೇಗ, ಒತ್ತಡ ಮತ್ತು ತಂಪಾಗಿಸುವ ವಿಧಾನಗಳಂತಹ ಅಂಶಗಳಿಗೆ ಎಚ್ಚರಿಕೆಯಿಂದ ಗಮನ ನೀಡುವುದರಿಂದ ಮೈಕ್ರೋಕ್ರ್ಯಾಕ್ಗಳ ರಚನೆಯನ್ನು ಕಡಿಮೆ ಮಾಡಲು ಮತ್ತು ಪ್ರಕ್ರಿಯೆಯ ಒಟ್ಟಾರೆ ಇಳುವರಿಯನ್ನು ಸುಧಾರಿಸಲು ಸಹಾಯ ಮಾಡುತ್ತದೆ. ಹೆಚ್ಚುವರಿಯಾಗಿ, ಲೇಸರ್ ಡೈಸಿಂಗ್ನಂತಹ ಹೆಚ್ಚು ಮುಂದುವರಿದ ಕತ್ತರಿಸುವ ತಂತ್ರಜ್ಞಾನಗಳ ಕುರಿತು ನಡೆಯುತ್ತಿರುವ ಸಂಶೋಧನೆಯು ಈ ಸಮಸ್ಯೆಗಳನ್ನು ಮತ್ತಷ್ಟು ತಗ್ಗಿಸುವ ಮಾರ್ಗಗಳನ್ನು ಅನ್ವೇಷಿಸುತ್ತಿದೆ.
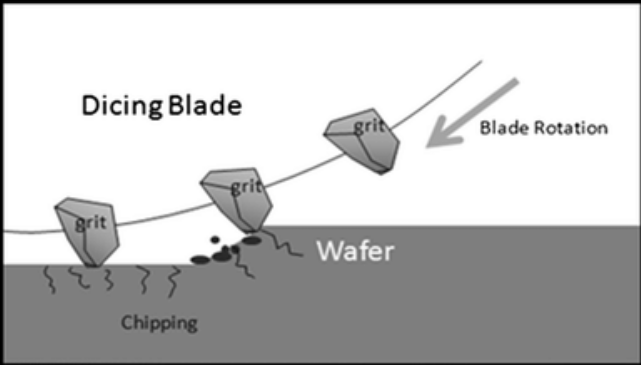
ದುರ್ಬಲವಾದ ವಸ್ತುವಾಗಿರುವುದರಿಂದ, ವೇಫರ್ಗಳು ಯಾಂತ್ರಿಕ, ಉಷ್ಣ ಅಥವಾ ರಾಸಾಯನಿಕ ಒತ್ತಡಕ್ಕೆ ಒಳಗಾದಾಗ ಆಂತರಿಕ ರಚನಾತ್ಮಕ ಬದಲಾವಣೆಗಳಿಗೆ ಗುರಿಯಾಗುತ್ತವೆ, ಇದು ಮೈಕ್ರೋಕ್ರ್ಯಾಕ್ಗಳ ರಚನೆಗೆ ಕಾರಣವಾಗುತ್ತದೆ. ಈ ಬಿರುಕುಗಳು ತಕ್ಷಣವೇ ಗಮನಕ್ಕೆ ಬಾರದಿದ್ದರೂ, ಉತ್ಪಾದನಾ ಪ್ರಕ್ರಿಯೆಯು ಮುಂದುವರೆದಂತೆ ಅವು ವಿಸ್ತರಿಸಬಹುದು ಮತ್ತು ಹೆಚ್ಚು ತೀವ್ರ ಹಾನಿಯನ್ನುಂಟುಮಾಡಬಹುದು. ನಂತರದ ಪ್ಯಾಕೇಜಿಂಗ್ ಮತ್ತು ಪರೀಕ್ಷಾ ಹಂತಗಳಲ್ಲಿ ಈ ಸಮಸ್ಯೆಯು ವಿಶೇಷವಾಗಿ ಸಮಸ್ಯಾತ್ಮಕವಾಗುತ್ತದೆ, ಅಲ್ಲಿ ತಾಪಮಾನದ ಏರಿಳಿತಗಳು ಮತ್ತು ಹೆಚ್ಚುವರಿ ಯಾಂತ್ರಿಕ ಒತ್ತಡಗಳು ಈ ಮೈಕ್ರೋಕ್ರ್ಯಾಕ್ಗಳು ಗೋಚರ ಮುರಿತಗಳಾಗಿ ವಿಕಸನಗೊಳ್ಳಲು ಕಾರಣವಾಗಬಹುದು, ಇದು ಚಿಪ್ ವೈಫಲ್ಯಕ್ಕೆ ಕಾರಣವಾಗಬಹುದು.
ಈ ಅಪಾಯವನ್ನು ತಗ್ಗಿಸಲು, ಕತ್ತರಿಸುವ ವೇಗ, ಒತ್ತಡ ಮತ್ತು ತಾಪಮಾನದಂತಹ ನಿಯತಾಂಕಗಳನ್ನು ಅತ್ಯುತ್ತಮವಾಗಿಸುವ ಮೂಲಕ ಕತ್ತರಿಸುವ ಪ್ರಕ್ರಿಯೆಯನ್ನು ಎಚ್ಚರಿಕೆಯಿಂದ ನಿಯಂತ್ರಿಸುವುದು ಅತ್ಯಗತ್ಯ. ಲೇಸರ್ ಡೈಸಿಂಗ್ನಂತಹ ಕಡಿಮೆ ಆಕ್ರಮಣಕಾರಿ ಕತ್ತರಿಸುವ ವಿಧಾನಗಳನ್ನು ಬಳಸುವುದರಿಂದ ವೇಫರ್ ಮೇಲಿನ ಯಾಂತ್ರಿಕ ಒತ್ತಡವನ್ನು ಕಡಿಮೆ ಮಾಡಬಹುದು ಮತ್ತು ಮೈಕ್ರೋಕ್ರ್ಯಾಕ್ಗಳ ರಚನೆಯನ್ನು ಕಡಿಮೆ ಮಾಡಬಹುದು. ಹೆಚ್ಚುವರಿಯಾಗಿ, ವೇಫರ್ ಡೈಸಿಂಗ್ ಪ್ರಕ್ರಿಯೆಯ ಸಮಯದಲ್ಲಿ ಇನ್ಫ್ರಾರೆಡ್ ಸ್ಕ್ಯಾನಿಂಗ್ ಅಥವಾ ಎಕ್ಸ್-ರೇ ಇಮೇಜಿಂಗ್ನಂತಹ ಸುಧಾರಿತ ತಪಾಸಣಾ ವಿಧಾನಗಳನ್ನು ಕಾರ್ಯಗತಗೊಳಿಸುವುದರಿಂದ ಈ ಆರಂಭಿಕ ಹಂತದ ಬಿರುಕುಗಳು ಹೆಚ್ಚಿನ ಹಾನಿಯನ್ನುಂಟುಮಾಡುವ ಮೊದಲು ಅವುಗಳನ್ನು ಪತ್ತೆಹಚ್ಚಲು ಸಹಾಯ ಮಾಡುತ್ತದೆ.
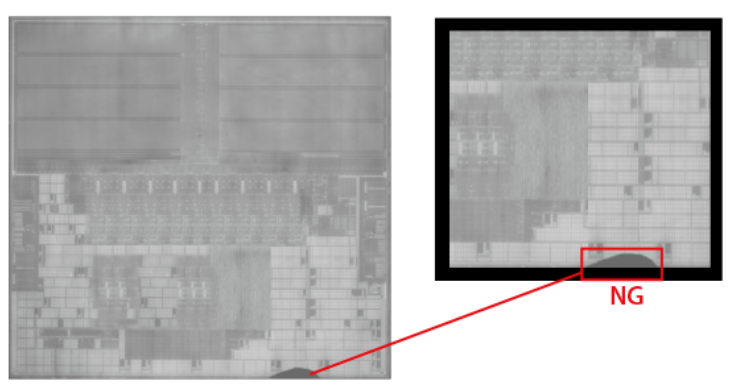
ವೇಫರ್ ಮೇಲ್ಮೈಗೆ ಆಗುವ ಹಾನಿಯು ಡೈಸಿಂಗ್ ಪ್ರಕ್ರಿಯೆಯಲ್ಲಿ ಗಮನಾರ್ಹ ಕಾಳಜಿಯಾಗಿದೆ, ಏಕೆಂದರೆ ಇದು ಚಿಪ್ನ ಕಾರ್ಯಕ್ಷಮತೆ ಮತ್ತು ವಿಶ್ವಾಸಾರ್ಹತೆಯ ಮೇಲೆ ನೇರ ಪರಿಣಾಮ ಬೀರುತ್ತದೆ. ಕತ್ತರಿಸುವ ಉಪಕರಣಗಳ ಅನುಚಿತ ಬಳಕೆ, ತಪ್ಪಾದ ಕತ್ತರಿಸುವ ನಿಯತಾಂಕಗಳು ಅಥವಾ ವೇಫರ್ನಲ್ಲಿಯೇ ಅಂತರ್ಗತವಾಗಿರುವ ವಸ್ತು ದೋಷಗಳಿಂದ ಅಂತಹ ಹಾನಿ ಉಂಟಾಗಬಹುದು. ಕಾರಣ ಏನೇ ಇರಲಿ, ಈ ಹಾನಿಗಳು ಸರ್ಕ್ಯೂಟ್ನ ವಿದ್ಯುತ್ ಪ್ರತಿರೋಧ ಅಥವಾ ಕೆಪಾಸಿಟನ್ಸ್ನಲ್ಲಿ ಬದಲಾವಣೆಗಳಿಗೆ ಕಾರಣವಾಗಬಹುದು, ಇದು ಒಟ್ಟಾರೆ ಕಾರ್ಯಕ್ಷಮತೆಯ ಮೇಲೆ ಪರಿಣಾಮ ಬೀರುತ್ತದೆ.
ಈ ಸಮಸ್ಯೆಗಳನ್ನು ಪರಿಹರಿಸಲು, ಎರಡು ಪ್ರಮುಖ ತಂತ್ರಗಳನ್ನು ಅನ್ವೇಷಿಸಲಾಗುತ್ತಿದೆ:
1. ಕತ್ತರಿಸುವ ಉಪಕರಣಗಳು ಮತ್ತು ನಿಯತಾಂಕಗಳನ್ನು ಅತ್ಯುತ್ತಮವಾಗಿಸುವುದು: ತೀಕ್ಷ್ಣವಾದ ಬ್ಲೇಡ್ಗಳನ್ನು ಬಳಸುವುದರಿಂದ, ಕತ್ತರಿಸುವ ವೇಗವನ್ನು ಸರಿಹೊಂದಿಸುವುದರಿಂದ ಮತ್ತು ಕತ್ತರಿಸುವ ಆಳವನ್ನು ಮಾರ್ಪಡಿಸುವುದರಿಂದ, ಕತ್ತರಿಸುವ ಪ್ರಕ್ರಿಯೆಯಲ್ಲಿ ಒತ್ತಡದ ಸಾಂದ್ರತೆಯನ್ನು ಕಡಿಮೆ ಮಾಡಬಹುದು, ಹೀಗಾಗಿ ಹಾನಿಯ ಸಾಮರ್ಥ್ಯವನ್ನು ಕಡಿಮೆ ಮಾಡಬಹುದು.
2. ಹೊಸ ಕತ್ತರಿಸುವ ತಂತ್ರಜ್ಞಾನಗಳನ್ನು ಅನ್ವೇಷಿಸುವುದು: ಲೇಸರ್ ಕತ್ತರಿಸುವುದು ಮತ್ತು ಪ್ಲಾಸ್ಮಾ ಕತ್ತರಿಸುವಂತಹ ಸುಧಾರಿತ ತಂತ್ರಗಳು ಸುಧಾರಿತ ನಿಖರತೆಯನ್ನು ನೀಡುತ್ತವೆ ಮತ್ತು ವೇಫರ್ಗೆ ಉಂಟಾಗುವ ಹಾನಿಯ ಮಟ್ಟವನ್ನು ಸಂಭಾವ್ಯವಾಗಿ ಕಡಿಮೆ ಮಾಡುತ್ತದೆ. ವೇಫರ್ನ ಮೇಲಿನ ಉಷ್ಣ ಮತ್ತು ಯಾಂತ್ರಿಕ ಒತ್ತಡವನ್ನು ಕಡಿಮೆ ಮಾಡುವಾಗ ಹೆಚ್ಚಿನ ಕತ್ತರಿಸುವ ನಿಖರತೆಯನ್ನು ಸಾಧಿಸುವ ಮಾರ್ಗಗಳನ್ನು ಕಂಡುಹಿಡಿಯಲು ಈ ತಂತ್ರಜ್ಞಾನಗಳನ್ನು ಅಧ್ಯಯನ ಮಾಡಲಾಗುತ್ತಿದೆ.
ಉಷ್ಣ ಪ್ರಭಾವದ ಪ್ರದೇಶ ಮತ್ತು ಕಾರ್ಯಕ್ಷಮತೆಯ ಮೇಲೆ ಅದರ ಪರಿಣಾಮಗಳು
ಲೇಸರ್ ಮತ್ತು ಪ್ಲಾಸ್ಮಾ ಕತ್ತರಿಸುವಿಕೆಯಂತಹ ಉಷ್ಣ ಕತ್ತರಿಸುವ ಪ್ರಕ್ರಿಯೆಗಳಲ್ಲಿ, ಹೆಚ್ಚಿನ ತಾಪಮಾನವು ಅನಿವಾರ್ಯವಾಗಿ ವೇಫರ್ನ ಮೇಲ್ಮೈಯಲ್ಲಿ ಉಷ್ಣ ಪ್ರಭಾವ ವಲಯವನ್ನು ಸೃಷ್ಟಿಸುತ್ತದೆ. ತಾಪಮಾನದ ಇಳಿಜಾರು ಗಮನಾರ್ಹವಾಗಿರುವಂತಹ ಈ ಪ್ರದೇಶವು ವಸ್ತುವಿನ ಗುಣಲಕ್ಷಣಗಳನ್ನು ಬದಲಾಯಿಸಬಹುದು, ಇದು ಚಿಪ್ನ ಅಂತಿಮ ಕಾರ್ಯಕ್ಷಮತೆಯ ಮೇಲೆ ಪರಿಣಾಮ ಬೀರುತ್ತದೆ.
ಉಷ್ಣ ಪೀಡಿತ ವಲಯದ (TAZ) ಪರಿಣಾಮ:
ಸ್ಫಟಿಕ ರಚನೆ ಬದಲಾವಣೆಗಳು: ಹೆಚ್ಚಿನ ತಾಪಮಾನದಲ್ಲಿ, ವೇಫರ್ ವಸ್ತುವಿನೊಳಗಿನ ಪರಮಾಣುಗಳು ಮರುಜೋಡಣೆಗೊಳ್ಳಬಹುದು, ಇದು ಸ್ಫಟಿಕ ರಚನೆಯಲ್ಲಿ ವಿರೂಪಗಳನ್ನು ಉಂಟುಮಾಡುತ್ತದೆ. ಈ ವಿರೂಪತೆಯು ವಸ್ತುವನ್ನು ದುರ್ಬಲಗೊಳಿಸುತ್ತದೆ, ಅದರ ಯಾಂತ್ರಿಕ ಶಕ್ತಿ ಮತ್ತು ಸ್ಥಿರತೆಯನ್ನು ಕಡಿಮೆ ಮಾಡುತ್ತದೆ, ಇದು ಬಳಕೆಯ ಸಮಯದಲ್ಲಿ ಚಿಪ್ ವೈಫಲ್ಯದ ಅಪಾಯವನ್ನು ಹೆಚ್ಚಿಸುತ್ತದೆ.
ವಿದ್ಯುತ್ ಗುಣಲಕ್ಷಣಗಳಲ್ಲಿನ ಬದಲಾವಣೆಗಳು: ಹೆಚ್ಚಿನ ತಾಪಮಾನವು ಅರೆವಾಹಕ ವಸ್ತುಗಳಲ್ಲಿ ವಾಹಕ ಸಾಂದ್ರತೆ ಮತ್ತು ಚಲನಶೀಲತೆಯನ್ನು ಬದಲಾಯಿಸಬಹುದು, ಇದು ಚಿಪ್ನ ವಿದ್ಯುತ್ ವಾಹಕತೆ ಮತ್ತು ಪ್ರಸ್ತುತ ಪ್ರಸರಣ ದಕ್ಷತೆಯ ಮೇಲೆ ಪರಿಣಾಮ ಬೀರುತ್ತದೆ. ಈ ಬದಲಾವಣೆಗಳು ಚಿಪ್ ಕಾರ್ಯಕ್ಷಮತೆಯಲ್ಲಿ ಕುಸಿತಕ್ಕೆ ಕಾರಣವಾಗಬಹುದು, ಸಂಭಾವ್ಯವಾಗಿ ಅದು ಅದರ ಉದ್ದೇಶಿತ ಉದ್ದೇಶಕ್ಕೆ ಸೂಕ್ತವಲ್ಲದಂತಾಗುತ್ತದೆ.
ಈ ಪರಿಣಾಮಗಳನ್ನು ತಗ್ಗಿಸಲು, ಕತ್ತರಿಸುವ ಸಮಯದಲ್ಲಿ ತಾಪಮಾನವನ್ನು ನಿಯಂತ್ರಿಸುವುದು, ಕತ್ತರಿಸುವ ನಿಯತಾಂಕಗಳನ್ನು ಅತ್ಯುತ್ತಮವಾಗಿಸುವುದು ಮತ್ತು ಕೂಲಿಂಗ್ ಜೆಟ್ಗಳು ಅಥವಾ ನಂತರದ ಸಂಸ್ಕರಣಾ ಚಿಕಿತ್ಸೆಗಳಂತಹ ವಿಧಾನಗಳನ್ನು ಅನ್ವೇಷಿಸುವುದು ಉಷ್ಣ ಪ್ರಭಾವದ ವ್ಯಾಪ್ತಿಯನ್ನು ಕಡಿಮೆ ಮಾಡಲು ಮತ್ತು ವಸ್ತುವಿನ ಸಮಗ್ರತೆಯನ್ನು ಕಾಪಾಡಿಕೊಳ್ಳಲು ಅಗತ್ಯವಾದ ತಂತ್ರಗಳಾಗಿವೆ.
ಒಟ್ಟಾರೆಯಾಗಿ, ವೇಫರ್ ಡೈಸಿಂಗ್ ತಂತ್ರಜ್ಞಾನದಲ್ಲಿ ಮೈಕ್ರೋಕ್ರ್ಯಾಕ್ಗಳು ಮತ್ತು ಉಷ್ಣ ಪ್ರಭಾವ ವಲಯಗಳು ನಿರ್ಣಾಯಕ ಸವಾಲುಗಳಾಗಿವೆ. ಅರೆವಾಹಕ ಉತ್ಪನ್ನಗಳ ಗುಣಮಟ್ಟವನ್ನು ಸುಧಾರಿಸಲು ಮತ್ತು ಅವುಗಳ ಮಾರುಕಟ್ಟೆ ಸ್ಪರ್ಧಾತ್ಮಕತೆಯನ್ನು ಹೆಚ್ಚಿಸಲು ತಾಂತ್ರಿಕ ಪ್ರಗತಿಗಳು ಮತ್ತು ಗುಣಮಟ್ಟ ನಿಯಂತ್ರಣ ಕ್ರಮಗಳ ಜೊತೆಗೆ ನಿರಂತರ ಸಂಶೋಧನೆ ಅಗತ್ಯವಾಗುತ್ತದೆ.
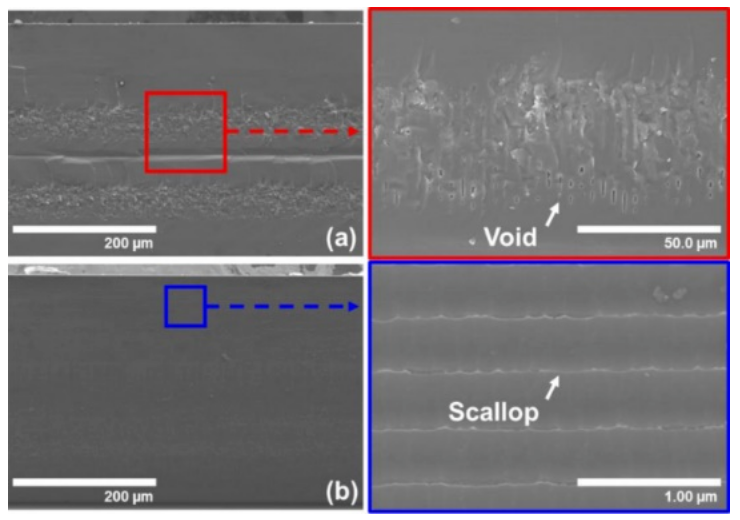
ಉಷ್ಣ ಪರಿಣಾಮ ವಲಯವನ್ನು ನಿಯಂತ್ರಿಸುವ ಕ್ರಮಗಳು:
ಕತ್ತರಿಸುವ ಪ್ರಕ್ರಿಯೆಯ ನಿಯತಾಂಕಗಳನ್ನು ಅತ್ಯುತ್ತಮವಾಗಿಸುವುದು: ಕತ್ತರಿಸುವ ವೇಗ ಮತ್ತು ಶಕ್ತಿಯನ್ನು ಕಡಿಮೆ ಮಾಡುವುದರಿಂದ ಉಷ್ಣ ಪ್ರಭಾವ ವಲಯದ (TAZ) ಗಾತ್ರವನ್ನು ಪರಿಣಾಮಕಾರಿಯಾಗಿ ಕಡಿಮೆ ಮಾಡಬಹುದು. ಕತ್ತರಿಸುವ ಪ್ರಕ್ರಿಯೆಯಲ್ಲಿ ಉತ್ಪತ್ತಿಯಾಗುವ ಶಾಖದ ಪ್ರಮಾಣವನ್ನು ನಿಯಂತ್ರಿಸಲು ಇದು ಸಹಾಯ ಮಾಡುತ್ತದೆ, ಇದು ವೇಫರ್ನ ವಸ್ತು ಗುಣಲಕ್ಷಣಗಳ ಮೇಲೆ ನೇರವಾಗಿ ಪರಿಣಾಮ ಬೀರುತ್ತದೆ.
ಸುಧಾರಿತ ಕೂಲಿಂಗ್ ತಂತ್ರಜ್ಞಾನಗಳು: ದ್ರವ ಸಾರಜನಕ ತಂಪಾಗಿಸುವಿಕೆ ಮತ್ತು ಮೈಕ್ರೋಫ್ಲೂಯಿಡಿಕ್ ತಂಪಾಗಿಸುವಿಕೆ ಮುಂತಾದ ತಂತ್ರಜ್ಞಾನಗಳ ಅನ್ವಯವು ಉಷ್ಣ ಪ್ರಭಾವ ವಲಯದ ವ್ಯಾಪ್ತಿಯನ್ನು ಗಮನಾರ್ಹವಾಗಿ ಮಿತಿಗೊಳಿಸುತ್ತದೆ. ಈ ತಂಪಾಗಿಸುವ ವಿಧಾನಗಳು ಶಾಖವನ್ನು ಹೆಚ್ಚು ಪರಿಣಾಮಕಾರಿಯಾಗಿ ಹೊರಹಾಕಲು ಸಹಾಯ ಮಾಡುತ್ತದೆ, ಹೀಗಾಗಿ ವೇಫರ್ನ ವಸ್ತು ಗುಣಲಕ್ಷಣಗಳನ್ನು ಸಂರಕ್ಷಿಸುತ್ತದೆ ಮತ್ತು ಉಷ್ಣ ಹಾನಿಯನ್ನು ಕಡಿಮೆ ಮಾಡುತ್ತದೆ.
ವಸ್ತು ಆಯ್ಕೆ: ಸಂಶೋಧಕರು ಅತ್ಯುತ್ತಮ ಉಷ್ಣ ವಾಹಕತೆ ಮತ್ತು ಯಾಂತ್ರಿಕ ಶಕ್ತಿಯನ್ನು ಹೊಂದಿರುವ ಕಾರ್ಬನ್ ನ್ಯಾನೊಟ್ಯೂಬ್ಗಳು ಮತ್ತು ಗ್ರ್ಯಾಫೀನ್ನಂತಹ ಹೊಸ ವಸ್ತುಗಳನ್ನು ಅನ್ವೇಷಿಸುತ್ತಿದ್ದಾರೆ. ಈ ವಸ್ತುಗಳು ಚಿಪ್ಗಳ ಒಟ್ಟಾರೆ ಕಾರ್ಯಕ್ಷಮತೆಯನ್ನು ಸುಧಾರಿಸುವಾಗ ಉಷ್ಣ ಪ್ರಭಾವ ವಲಯವನ್ನು ಕಡಿಮೆ ಮಾಡಬಹುದು.
ಸಂಕ್ಷಿಪ್ತವಾಗಿ ಹೇಳುವುದಾದರೆ, ಉಷ್ಣ ಪ್ರಭಾವ ವಲಯವು ಉಷ್ಣ ಕತ್ತರಿಸುವ ತಂತ್ರಜ್ಞಾನಗಳ ಅನಿವಾರ್ಯ ಪರಿಣಾಮವಾಗಿದ್ದರೂ, ಅದನ್ನು ಅತ್ಯುತ್ತಮ ಸಂಸ್ಕರಣಾ ತಂತ್ರಗಳು ಮತ್ತು ವಸ್ತು ಆಯ್ಕೆಯ ಮೂಲಕ ಪರಿಣಾಮಕಾರಿಯಾಗಿ ನಿಯಂತ್ರಿಸಬಹುದು. ಭವಿಷ್ಯದ ಸಂಶೋಧನೆಯು ಹೆಚ್ಚು ಪರಿಣಾಮಕಾರಿ ಮತ್ತು ನಿಖರವಾದ ವೇಫರ್ ಡೈಸಿಂಗ್ ಅನ್ನು ಸಾಧಿಸಲು ಫೈನ್-ಟ್ಯೂನಿಂಗ್ ಮತ್ತು ಥರ್ಮಲ್ ಕತ್ತರಿಸುವ ಪ್ರಕ್ರಿಯೆಗಳನ್ನು ಸ್ವಯಂಚಾಲಿತಗೊಳಿಸುವುದರ ಮೇಲೆ ಕೇಂದ್ರೀಕರಿಸುತ್ತದೆ.

ಸಮತೋಲನ ತಂತ್ರ:
ವೇಫರ್ ಇಳುವರಿ ಮತ್ತು ಉತ್ಪಾದನಾ ದಕ್ಷತೆಯ ನಡುವಿನ ಅತ್ಯುತ್ತಮ ಸಮತೋಲನವನ್ನು ಸಾಧಿಸುವುದು ವೇಫರ್ ಡೈಸಿಂಗ್ ತಂತ್ರಜ್ಞಾನದಲ್ಲಿ ನಿರಂತರ ಸವಾಲಾಗಿದೆ. ತರ್ಕಬದ್ಧ ಉತ್ಪಾದನಾ ತಂತ್ರ ಮತ್ತು ಪ್ರಕ್ರಿಯೆಯ ನಿಯತಾಂಕಗಳನ್ನು ಅಭಿವೃದ್ಧಿಪಡಿಸಲು ತಯಾರಕರು ಮಾರುಕಟ್ಟೆ ಬೇಡಿಕೆ, ಉತ್ಪಾದನಾ ವೆಚ್ಚಗಳು ಮತ್ತು ಉತ್ಪನ್ನದ ಗುಣಮಟ್ಟದಂತಹ ಬಹು ಅಂಶಗಳನ್ನು ಪರಿಗಣಿಸಬೇಕಾಗುತ್ತದೆ. ಅದೇ ಸಮಯದಲ್ಲಿ, ಸುಧಾರಿತ ಕತ್ತರಿಸುವ ಉಪಕರಣಗಳನ್ನು ಪರಿಚಯಿಸುವುದು, ನಿರ್ವಾಹಕ ಕೌಶಲ್ಯಗಳನ್ನು ಸುಧಾರಿಸುವುದು ಮತ್ತು ಕಚ್ಚಾ ವಸ್ತುಗಳ ಗುಣಮಟ್ಟ ನಿಯಂತ್ರಣವನ್ನು ಹೆಚ್ಚಿಸುವುದು ಉತ್ಪಾದನಾ ದಕ್ಷತೆಯನ್ನು ಹೆಚ್ಚಿಸುವಾಗ ಇಳುವರಿಯನ್ನು ಕಾಪಾಡಿಕೊಳ್ಳಲು ಅಥವಾ ಸುಧಾರಿಸಲು ಅತ್ಯಗತ್ಯ.
ಭವಿಷ್ಯದ ಸವಾಲುಗಳು ಮತ್ತು ಅವಕಾಶಗಳು:
ಅರೆವಾಹಕ ತಂತ್ರಜ್ಞಾನದ ಪ್ರಗತಿಯೊಂದಿಗೆ, ವೇಫರ್ ಕತ್ತರಿಸುವಿಕೆಯು ಹೊಸ ಸವಾಲುಗಳು ಮತ್ತು ಅವಕಾಶಗಳನ್ನು ಎದುರಿಸುತ್ತಿದೆ. ಚಿಪ್ ಗಾತ್ರಗಳು ಕುಗ್ಗುತ್ತಿದ್ದಂತೆ ಮತ್ತು ಏಕೀಕರಣ ಹೆಚ್ಚಾದಂತೆ, ಕತ್ತರಿಸುವ ನಿಖರತೆ ಮತ್ತು ಗುಣಮಟ್ಟದ ಮೇಲಿನ ಬೇಡಿಕೆಗಳು ಗಮನಾರ್ಹವಾಗಿ ಬೆಳೆಯುತ್ತವೆ. ಅದೇ ಸಮಯದಲ್ಲಿ, ಉದಯೋನ್ಮುಖ ತಂತ್ರಜ್ಞಾನಗಳು ವೇಫರ್ ಕತ್ತರಿಸುವ ತಂತ್ರಗಳ ಅಭಿವೃದ್ಧಿಗೆ ಹೊಸ ಆಲೋಚನೆಗಳನ್ನು ಒದಗಿಸುತ್ತವೆ. ತಯಾರಕರು ಮಾರುಕಟ್ಟೆ ಚಲನಶೀಲತೆ ಮತ್ತು ತಾಂತ್ರಿಕ ಪ್ರವೃತ್ತಿಗಳಿಗೆ ಅನುಗುಣವಾಗಿರಬೇಕು, ಮಾರುಕಟ್ಟೆ ಬದಲಾವಣೆಗಳು ಮತ್ತು ತಾಂತ್ರಿಕ ಬೇಡಿಕೆಗಳನ್ನು ಪೂರೈಸಲು ಉತ್ಪಾದನಾ ತಂತ್ರಗಳು ಮತ್ತು ಪ್ರಕ್ರಿಯೆಯ ನಿಯತಾಂಕಗಳನ್ನು ನಿರಂತರವಾಗಿ ಸರಿಹೊಂದಿಸಬೇಕು ಮತ್ತು ಅತ್ಯುತ್ತಮವಾಗಿಸಬೇಕು.
ಕೊನೆಯಲ್ಲಿ, ಮಾರುಕಟ್ಟೆ ಬೇಡಿಕೆ, ಉತ್ಪಾದನಾ ವೆಚ್ಚಗಳು ಮತ್ತು ಉತ್ಪನ್ನದ ಗುಣಮಟ್ಟವನ್ನು ಪರಿಗಣಿಸುವ ಮೂಲಕ ಮತ್ತು ಸುಧಾರಿತ ಉಪಕರಣಗಳು ಮತ್ತು ತಂತ್ರಜ್ಞಾನವನ್ನು ಪರಿಚಯಿಸುವ ಮೂಲಕ, ಆಪರೇಟರ್ ಕೌಶಲ್ಯಗಳನ್ನು ಹೆಚ್ಚಿಸುವ ಮೂಲಕ ಮತ್ತು ಕಚ್ಚಾ ವಸ್ತುಗಳ ನಿಯಂತ್ರಣವನ್ನು ಬಲಪಡಿಸುವ ಮೂಲಕ, ತಯಾರಕರು ವೇಫರ್ ಡೈಸಿಂಗ್ ಸಮಯದಲ್ಲಿ ವೇಫರ್ ಇಳುವರಿ ಮತ್ತು ಉತ್ಪಾದನಾ ದಕ್ಷತೆಯ ನಡುವೆ ಉತ್ತಮ ಸಮತೋಲನವನ್ನು ಸಾಧಿಸಬಹುದು, ಇದು ದಕ್ಷ ಮತ್ತು ಉತ್ತಮ-ಗುಣಮಟ್ಟದ ಅರೆವಾಹಕ ಉತ್ಪನ್ನ ಉತ್ಪಾದನೆಗೆ ಕಾರಣವಾಗುತ್ತದೆ.
ಭವಿಷ್ಯದ ದೃಷ್ಟಿಕೋನ:
ತ್ವರಿತ ತಾಂತ್ರಿಕ ಪ್ರಗತಿಯೊಂದಿಗೆ, ಅರೆವಾಹಕ ತಂತ್ರಜ್ಞಾನವು ಅಭೂತಪೂರ್ವ ವೇಗದಲ್ಲಿ ಪ್ರಗತಿ ಸಾಧಿಸುತ್ತಿದೆ. ಅರೆವಾಹಕ ಉತ್ಪಾದನೆಯಲ್ಲಿ ನಿರ್ಣಾಯಕ ಹೆಜ್ಜೆಯಾಗಿ, ವೇಫರ್ ಕತ್ತರಿಸುವ ತಂತ್ರಜ್ಞಾನವು ಹೊಸ ಅತ್ಯಾಕರ್ಷಕ ಬೆಳವಣಿಗೆಗಳಿಗೆ ಸಿದ್ಧವಾಗಿದೆ. ಮುಂದೆ ನೋಡುವಾಗ, ವೇಫರ್ ಕತ್ತರಿಸುವ ತಂತ್ರಜ್ಞಾನವು ನಿಖರತೆ, ದಕ್ಷತೆ ಮತ್ತು ವೆಚ್ಚದಲ್ಲಿ ಗಮನಾರ್ಹ ಸುಧಾರಣೆಗಳನ್ನು ಸಾಧಿಸುವ ನಿರೀಕ್ಷೆಯಿದೆ, ಅರೆವಾಹಕ ಉದ್ಯಮದ ನಿರಂತರ ಬೆಳವಣಿಗೆಗೆ ಹೊಸ ಚೈತನ್ಯವನ್ನು ತುಂಬುತ್ತದೆ.
ಹೆಚ್ಚುತ್ತಿರುವ ನಿಖರತೆ:
ಹೆಚ್ಚಿನ ನಿಖರತೆಯ ಅನ್ವೇಷಣೆಯಲ್ಲಿ, ವೇಫರ್ ಕತ್ತರಿಸುವ ತಂತ್ರಜ್ಞಾನವು ಅಸ್ತಿತ್ವದಲ್ಲಿರುವ ಪ್ರಕ್ರಿಯೆಗಳ ಮಿತಿಗಳನ್ನು ನಿರಂತರವಾಗಿ ತಳ್ಳುತ್ತದೆ. ಕತ್ತರಿಸುವ ಪ್ರಕ್ರಿಯೆಯ ಭೌತಿಕ ಮತ್ತು ರಾಸಾಯನಿಕ ಕಾರ್ಯವಿಧಾನಗಳನ್ನು ಆಳವಾಗಿ ಅಧ್ಯಯನ ಮಾಡುವ ಮೂಲಕ ಮತ್ತು ಕತ್ತರಿಸುವ ನಿಯತಾಂಕಗಳನ್ನು ನಿಖರವಾಗಿ ನಿಯಂತ್ರಿಸುವ ಮೂಲಕ, ಹೆಚ್ಚು ಸಂಕೀರ್ಣವಾದ ಸರ್ಕ್ಯೂಟ್ ವಿನ್ಯಾಸದ ಅವಶ್ಯಕತೆಗಳನ್ನು ಪೂರೈಸಲು ಉತ್ತಮವಾದ ಕತ್ತರಿಸುವ ಫಲಿತಾಂಶಗಳನ್ನು ಸಾಧಿಸಲಾಗುತ್ತದೆ. ಹೆಚ್ಚುವರಿಯಾಗಿ, ಹೊಸ ವಸ್ತುಗಳ ಪರಿಶೋಧನೆ ಮತ್ತು ಕತ್ತರಿಸುವ ವಿಧಾನಗಳು ಇಳುವರಿ ಮತ್ತು ಗುಣಮಟ್ಟವನ್ನು ಗಮನಾರ್ಹವಾಗಿ ಸುಧಾರಿಸುತ್ತದೆ.
ದಕ್ಷತೆಯನ್ನು ಹೆಚ್ಚಿಸುವುದು:
ಹೊಸ ವೇಫರ್ ಕತ್ತರಿಸುವ ಉಪಕರಣಗಳು ಸ್ಮಾರ್ಟ್ ಮತ್ತು ಸ್ವಯಂಚಾಲಿತ ವಿನ್ಯಾಸದ ಮೇಲೆ ಕೇಂದ್ರೀಕರಿಸುತ್ತವೆ. ಸುಧಾರಿತ ನಿಯಂತ್ರಣ ವ್ಯವಸ್ಥೆಗಳು ಮತ್ತು ಅಲ್ಗಾರಿದಮ್ಗಳ ಪರಿಚಯವು ವಿಭಿನ್ನ ವಸ್ತುಗಳು ಮತ್ತು ವಿನ್ಯಾಸ ಅವಶ್ಯಕತೆಗಳನ್ನು ಪೂರೈಸಲು ಉಪಕರಣಗಳು ಕತ್ತರಿಸುವ ನಿಯತಾಂಕಗಳನ್ನು ಸ್ವಯಂಚಾಲಿತವಾಗಿ ಹೊಂದಿಸಲು ಅನುವು ಮಾಡಿಕೊಡುತ್ತದೆ, ಹೀಗಾಗಿ ಉತ್ಪಾದನಾ ದಕ್ಷತೆಯನ್ನು ಗಮನಾರ್ಹವಾಗಿ ಸುಧಾರಿಸುತ್ತದೆ. ಮಲ್ಟಿ-ವೇಫರ್ ಕತ್ತರಿಸುವ ತಂತ್ರಜ್ಞಾನ ಮತ್ತು ಕ್ಷಿಪ್ರ ಬ್ಲೇಡ್ ಬದಲಿ ವ್ಯವಸ್ಥೆಗಳಂತಹ ನಾವೀನ್ಯತೆಗಳು ದಕ್ಷತೆಯನ್ನು ಹೆಚ್ಚಿಸುವಲ್ಲಿ ನಿರ್ಣಾಯಕ ಪಾತ್ರ ವಹಿಸುತ್ತವೆ.
ವೆಚ್ಚ ಕಡಿತ:
ವೇಫರ್ ಕತ್ತರಿಸುವ ತಂತ್ರಜ್ಞಾನದ ಅಭಿವೃದ್ಧಿಗೆ ವೆಚ್ಚವನ್ನು ಕಡಿಮೆ ಮಾಡುವುದು ಒಂದು ಪ್ರಮುಖ ನಿರ್ದೇಶನವಾಗಿದೆ. ಹೊಸ ವಸ್ತುಗಳು ಮತ್ತು ಕತ್ತರಿಸುವ ವಿಧಾನಗಳನ್ನು ಅಭಿವೃದ್ಧಿಪಡಿಸಿದಂತೆ, ಸಲಕರಣೆಗಳ ವೆಚ್ಚಗಳು ಮತ್ತು ನಿರ್ವಹಣಾ ವೆಚ್ಚಗಳನ್ನು ಪರಿಣಾಮಕಾರಿಯಾಗಿ ನಿಯಂತ್ರಿಸುವ ನಿರೀಕ್ಷೆಯಿದೆ. ಹೆಚ್ಚುವರಿಯಾಗಿ, ಉತ್ಪಾದನಾ ಪ್ರಕ್ರಿಯೆಗಳನ್ನು ಉತ್ತಮಗೊಳಿಸುವುದು ಮತ್ತು ಸ್ಕ್ರ್ಯಾಪ್ ದರಗಳನ್ನು ಕಡಿಮೆ ಮಾಡುವುದರಿಂದ ಉತ್ಪಾದನೆಯ ಸಮಯದಲ್ಲಿ ತ್ಯಾಜ್ಯವನ್ನು ಮತ್ತಷ್ಟು ಕಡಿಮೆ ಮಾಡುತ್ತದೆ, ಇದು ಒಟ್ಟಾರೆ ಉತ್ಪಾದನಾ ವೆಚ್ಚದಲ್ಲಿ ಇಳಿಕೆಗೆ ಕಾರಣವಾಗುತ್ತದೆ.
ಸ್ಮಾರ್ಟ್ ಉತ್ಪಾದನೆ ಮತ್ತು IoT:
ಸ್ಮಾರ್ಟ್ ಉತ್ಪಾದನೆ ಮತ್ತು ಇಂಟರ್ನೆಟ್ ಆಫ್ ಥಿಂಗ್ಸ್ (IoT) ತಂತ್ರಜ್ಞಾನಗಳ ಏಕೀಕರಣವು ವೇಫರ್ ಕತ್ತರಿಸುವ ತಂತ್ರಜ್ಞಾನದಲ್ಲಿ ಪರಿವರ್ತನಾತ್ಮಕ ಬದಲಾವಣೆಗಳನ್ನು ತರುತ್ತದೆ. ಸಾಧನಗಳ ನಡುವಿನ ಪರಸ್ಪರ ಸಂಪರ್ಕ ಮತ್ತು ಡೇಟಾ ಹಂಚಿಕೆಯ ಮೂಲಕ, ಉತ್ಪಾದನಾ ಪ್ರಕ್ರಿಯೆಯ ಪ್ರತಿಯೊಂದು ಹಂತವನ್ನು ನೈಜ ಸಮಯದಲ್ಲಿ ಮೇಲ್ವಿಚಾರಣೆ ಮಾಡಬಹುದು ಮತ್ತು ಅತ್ಯುತ್ತಮವಾಗಿಸಬಹುದು. ಇದು ಉತ್ಪಾದನಾ ದಕ್ಷತೆ ಮತ್ತು ಉತ್ಪನ್ನದ ಗುಣಮಟ್ಟವನ್ನು ಸುಧಾರಿಸುವುದಲ್ಲದೆ, ಕಂಪನಿಗಳಿಗೆ ಹೆಚ್ಚು ನಿಖರವಾದ ಮಾರುಕಟ್ಟೆ ಮುನ್ಸೂಚನೆ ಮತ್ತು ನಿರ್ಧಾರ ತೆಗೆದುಕೊಳ್ಳುವ ಬೆಂಬಲವನ್ನು ಒದಗಿಸುತ್ತದೆ.
ಭವಿಷ್ಯದಲ್ಲಿ, ವೇಫರ್ ಕತ್ತರಿಸುವ ತಂತ್ರಜ್ಞಾನವು ನಿಖರತೆ, ದಕ್ಷತೆ ಮತ್ತು ವೆಚ್ಚದಲ್ಲಿ ಗಮನಾರ್ಹ ಪ್ರಗತಿಯನ್ನು ಸಾಧಿಸುತ್ತದೆ. ಈ ಪ್ರಗತಿಗಳು ಅರೆವಾಹಕ ಉದ್ಯಮದ ನಿರಂತರ ಅಭಿವೃದ್ಧಿಯನ್ನು ಚಾಲನೆ ಮಾಡುತ್ತವೆ ಮತ್ತು ಮಾನವ ಸಮಾಜಕ್ಕೆ ಹೆಚ್ಚಿನ ತಾಂತ್ರಿಕ ಆವಿಷ್ಕಾರಗಳು ಮತ್ತು ಅನುಕೂಲಗಳನ್ನು ತರುತ್ತವೆ.
ಪೋಸ್ಟ್ ಸಮಯ: ನವೆಂಬರ್-19-2024